Is Nearshore Sourcing the Future of Discrete Manufacturing?
Is Nearshore Sourcing the Future of Discrete Manufacturing?
Is Nearshore Sourcing the Future of Discrete Manufacturing?
Sept 27, 2021
Jim Tuttle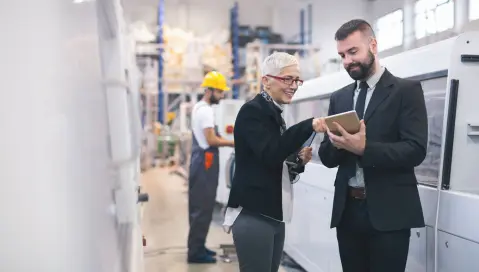
Clearly, the COVID-19 pandemic had a seismic impact on global supply chains. But while many sectors are now in recovery, for discrete manufacturers, component availability remains an ongoing issue. Continued production and transportation delays in some of the world’s key regions are delaying customer orders and driving up material prices. And it’s forcing many discrete manufacturing companies to think outside the box. With uncertainty now the only certainty, the time has come to reassess where organizations source parts from, and potentially look closer to home. Could nearshore sourcing be the future of discrete manufacturing? Let’s explore…
Just In Time Manufacturing Hit by Pandemic Supply Shortages
One of the major issues with discrete manufacturing is that the sector has flourished on a just in time (JIT) production model, but this approach is vulnerable to market disruption. During the height of the pandemic, many manufacturers paid the price for JIT. As component production stalled and freight logistics slowed, parts were running out before they could be replenished. And that was a best case scenario. For some discrete manufacturers, trusted component sources collapsed altogether. The automobile industry was particularly badly hit, as a combination of COVID-19 setbacks (caused by increased consumer electronics demand for semiconductors) and a major fire at Japan’s Renasas Electronics factory in March squeezed global computer chip supplies. With around 30% of the world’s vehicle microcontroller unit chips supplied by Renasas, Ford, GM, Honda, Mercedes-Benz and Nissan were among the major automobile brands whose production capabilities were hit; even brought to a temporary standstill. A recent Time magazine article looked at the prospect of solving this problem through local production. And, while it concluded that chip manufacturing still depends on global resources, it noted that the U.S. Innovation and Competition Act, launched in June, will support domestic investment in component production capabilities. The West may never overtake Asia in volume and sophistication, but it could grow to a point where nearshore computer chip sourcing becomes a viable alternative.
Localize Sourcing To Increase Supply Chain Resilience
Automotive manufacturing isn’t the only sector looking at nearshore supply networks. New Deloitte data has shown that post-pandemic, 4 in 10 businesses want to localize their supply chain to increase reliability. The focus on dependability and resilience is key to this shift. Nearshore sourcing won’t often be the cheapest option. However, if the failure of JIT production models during the COVID-19 pandemic taught us anything, it’s that the cheapest option won’t always serve you best. For discrete manufacturers, the industry’s future will be built on a careful balance between running lean and preparing for ‘just in case’ scenarios. And part of this strategy involves widening supply networks, to source goods from not only different suppliers, but different geographical regions.
Ultimately, it may even involve leveraging the local manufacturing community to enable nearshore production. In a recent Supply Chain Management Review article, Wikifactory Co-Founder, Nicolai Peitersen, discussed a future in which manufacturers use the Internet of Production as their go-to model. Utilizing digital technology and virtual networks to connect organizations and produce physical products in a cost-effective way with a low eco-footprint.
Matching Supplier Insight With Operational Needs
While the Internet of Production may be a giant leap from many discrete manufacturers’ current capabilities, the idea of adding new suppliers seems a logical next step. But mitigating future availability issues is not as simple as just expanding your little black book. To truly strengthen your supply network, manufacturers need complete visibility over all your supplier options, their location and their capabilities, to create a shortlist of relevant options. You also need to understand the availability and lead times of each supplier, so you can factor this into your production schedule. Discrete manufacturing ERP technology empowers organizations to manage supply networks transparently, so you can build valuable long-term relationships with primary and secondary suppliers. More importantly, it connects your operational data with inventory needs—so you can schedule production around component availability and vice versa. By using manufacturing ERP software to run your business, you’ll have both the insight to select suppliers based on upcoming work orders and market conditions, and the flexibility to choose alternative options if those conditions change. It’s up to you whether you focus on the most affordable source of supply, or nearshore options that are more expensive, but closer to home. Offshore or local, building a resilient, agile supply chain that can weather future disruption depends on understanding your operational needs in real time, and syncing this with supplier availability. And, however you choose to diversify your supplier database, discrete manufacturing ERP software can integrate these critical business areas. For more insights, download our new whitepaper: Strength and Stretch: Increasing Resilience and Agility in your Manufacturing Supply Chain.
Or book an Aptean Industrial Manufacturing ERP demo to improve your supply chain management.
Empieza a transformar tu empresa hoy mismo
Si estás listo para llevar tu negocio de producción industrial al siguiente nivel, nos encantaría ayudarte
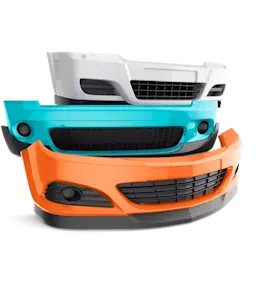