Manage and Mitigate the Risk of Product Recalls With Process Manufacturing ERP
Manage and Mitigate the Risk of Product Recalls With Process Manufacturing ERP
Manage and Mitigate the Risk of Product Recalls With Process Manufacturing ERP
Jun 17, 2021
Daniel Erickson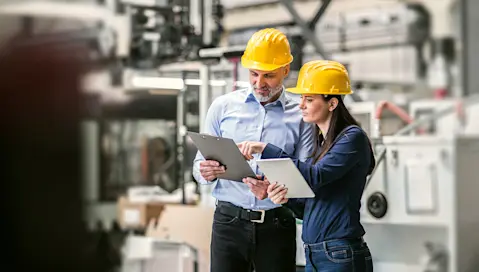
There’s a famous Hollywood saying that you’re only as good as your last performance. In manufacturing, you’re only as good as your latest output—and a product recall can severely damage that status.
For process manufacturers, the biggest impact is often not caused by the recall itself, but in the way that recall is handled. Especially, if it takes too long to identify the source of the problem and locate all those goods affected. Sometimes, more products than necessary are recalled, just to ensure the problem is resolved. And the scale and speed of these recalls can significantly impact customer confidence.
What can process manufacturers do to manage product recalls more effectively, limiting their financial and reputational effects? Here are some suggestions…
Why Are Product Recalls So Problematic for Process Manufacturers?
While every type of manufacturing business is affected by product recalls, the reputational risk is particularly high for process manufacturers. Why?
Firstly, large batch manufacturing means a huge number of products can be affected by one recall, as goods have been distributed to a wide number of customers. One simple error such as cross-contamination between ingredients, or contamination in the process plant, can lead to thousands of products being recalled.
Secondly, the potential reach of sub-standard products makes locating and returning them a major logistical challenge. Process manufacturers need to understand what lots have been affected by a production issue, and where those products have been distributed, to take control of a recall initiative quickly.
Thirdly, many of the sectors that process manufacturers operate in are tightly regulated—so even a simple admin mistake, which doesn’t impact the actual product quality—can result in a recall. Improper labelling or missing information on the certificate of analysis (CofA) are good examples of this.
Finally, the reputational and financial impact of a product recall is significant when you’re dealing with products that could be harmful if used or consumed when the recipe isn’t followed precisely. Look no further than hand sanitizer manufacturing during the pandemic as a pertinent example.
The Food and Drug Administration (FDA) has recalled at least 75 hand sanitizer brands labelled to contain ethanol/ethyl alcohol, but which tested positive for methanol (wood alcohol). If consumers absorb methanol through their skin, the reaction can cause blindness and even result in death if ingested. Nobody wants to be responsible for manufacturing and circulating lethal products.
How Can Manufacturers React Quickly to Product Recalls?
The best way to avoid product recalls is not to need them in the first place, and there are numerous things that process manufacturers can do to reduce the risk of production and compliance issues.
The single most powerful way to improve quality control and manufacturing consistency is to invest in enterprise resource planning (ERP) software. As this will increases the visibility and accountability of every ingredient and process.
Most manufacturers think of ERP technology as optimizing processes, but it also plays a valuable role in minimizing product recalls—helping organizations to get ahead of an issue quickly by increasing traceability.
Selecting an ERP solution with built-in traceability features enables process manufacturers to track and account for every raw ingredient or material used, from supply to finished goods. So, if there is a quality control issue, you can quickly identify the source along with a list of customers who purchased affected lots, whether those orders have been produced, and where completed orders have been shipped.
Process manufacturing ERP software integrates inventory information with your bill of materials, batch tickets, lot numbers and bill of lading, along with product line information and storage locations. Within seconds, it’s possible to view a digital footprint of your recall’s reach. And with this information in hand, you can put the wheels in motion to recall affected products.
How Can Process Manufacturing ERP Software Reduce the Financial Impact of Product Recalls?
There’s no avoiding the fact that product recalls are expensive because they hit process manufacturers twice. Firstly, the original batch of goods is null and void, and will need to be replaced to the customer free of charge. Secondly, the logistics of identifying non-compliant products and getting them back to the plant is expensive.
The direct costs involved in a product recall include production stoppage (and then overtime to replace contaminated goods), laboratory testing, legal fines/penalties and return shipping. And that’s not factoring in the reputational impact of a high-profile product recall on customer orders, or the marketing and advertising push you need to invest in to restore people’s confidence.
Process manufacturing ERP software can help you manage and mitigate the expense of product recalls, using both proactive and reactive capabilities.
For example, mock recalls are an effective way to model what needs to happen during a real recall, to ensure that every single sub-standard product can be identified during a set period. Process manufacturing ERP technology can be used to assign duties, store plans, notify those involved, and evaluate the results of simulated scenarios, to refine procedures and improve your response times.
Additionally, ERP software will enhance compliance protocol to reduce the risk of major product recalls occurring. For example, Global Harmonizing System (GHS) and Safety Data Sheet (SDS) authoring ensures that comprehensive, accurate information related to every product and process is available business-wide. Improving these safety procedures and compliance checks can lead to potential issues being identified and rectified prior to production—and detailed records also enable recalled products to be identified quicker once they’ve been shipped.
If an issue has already occurred and a product needs to be recalled, advanced process manufacturing ERP software offers two built-in features that make this process speedier and simpler.
The first of these is a Warehouse Management System (WMS), which monitors and automates inventory transactions using barcode scanning capabilities. This barcode stores product data including lot numbers, storage locations and inventory movements, to track down work-in-progress (WIP) and finished goods affected by quality control or compliance issues.
The second critical feature, which we’ve already touched on, is trace capability; providing full visibility over the process manufacturing process—from raw materials to individual batches. ERP software gives your business forward and backward lot traceability, to accurately identify affected goods without pulling more products than necessary.
Detailed tracing capabilities are especially important for sectors that set time targets on product recalls, such as the chemical industry. They are also incredibly useful for supporting regulatory bodies like the FDA, which can require extensive product information to conduct voluntary or controlled product recalls.
Minimize the Impact of a Product Recall
Prevention is always better than cure, and process manufacturing ERP technology helps you minimize the risk of product recalls and plan effective response processes. But if the worst-case scenario happens and quality control issues occur, having ERP software in place is a game-changer for your organization.
As soon as the clock starts ticking, ERP gives you the complete visibility and traceability required to locate the exact source of the problem and see what goods have been affected—at every production stage. Those products can be pulled from the supply chain as quickly as possible, minimizing the financial and reputational impact on your overall operations.
Aptean Process Manufacturing ERP is a fully integrated solution, streamlining workflow and providing scalable, flexible functionality—including product recalls.
To protect your reputation, talk to us about how Aptean’s cloud ERP technology can improve quality control and enable end-to end traceability. Request a free demo of our process manufacturing software and learn how to be recall ready.
¿Todo listo para transformar tu negocio?
Tenemos las soluciones ERP especializadas que necesitas para superar los desafíos de tu sector.
