Destacado en este post
What Is EAM Software and Why Do You Need It?
What Is EAM Software and Why Do You Need It?
Ago 30, 2022
Kay Jenkins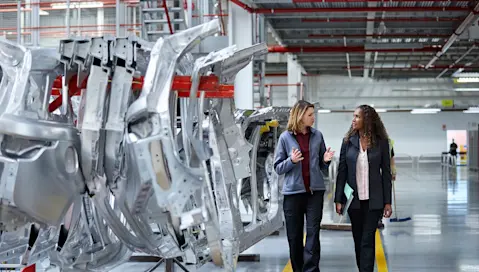
If you’re a business owner or maintenance manager of an asset-intensive business, you may have been operating on a reactive maintenance schedule and short term, quick fixes. While this type of maintenance plan may have worked in the past, using these strategies will hamper long-term growth and success. Instead, you need an asset lifecycle management strategy to support peak production and get the most out of your assets.
If you don’t know what you’re spending on maintenance, and when and where maintenance activities are occurring, chances are you’re not as productive as you could be. In this article, we’ll examine the best way to handle asset lifecycle management, and how to avoid common pitfalls that are holding you back.
We’ll discuss the benefits of this approach and consider how to successfully implement a long-term asset lifecycle management strategy. We’ll also talk about how technology—namely, enterprise asset management (EAM) software—can help you navigate the four stages of asset lifecycle management.
What Is EAM Software?
EAM, or enterprise asset management, software, is a set of tools used to track and manage physical assets throughout their lifecycle. Asset-intensive businesses like yours have made significant investments in their property and equipment which means you need to keep those assets in tip-top shape. EAM software is designed to help you do that by enabling you to plan, optimize, execute and track all maintenance activities—keeping production humming.
A robust EAM system can help your business in multiple ways. It can:
Increase performance and uptime of assets
Extend the life of assets
Reduce operational costs, particularly around maintenance and labor
Streamline all activities related to asset management, enabling you to get more done with existing, or even fewer, resources
Help with audit and regulatory compliance
The analysts at Gartner research define EAM software as a set of tools that focus on maintaining an accurate, detailed database of physical assets with maintenance history and documents. Some EAM software solutions include inventory management and analytics tools. An EAM supports preventive asset maintenance through scheduled tasks based on historical records or original equipment manufacturer (OEM) vendor guidance.
For a more thorough overview of EAM software, its features and benefits, be sure to read our guide to EAM.
What Is Asset Lifecycle Management (ALM)?
The asset lifecycle is just what it sounds like—it refers to the lifecycle of an asset from procurement to disposal. Asset lifecycle management, or ALM, is the management of this process so that you know how the asset is purchased, maintained and replaced once it reaches the end of its useful life.
Most experts agree that the asset lifecycle can be broken out into four stages.
Planning
Acquisition and deployment
Operation and maintenance
Asset Disposal
The purpose of ALM is to maximize the useful life of critical assets. Sounds easy enough, but if your maintenance team is trying to manage your assets with paper-based processes or a series of spreadsheets, you’ll never meet that goal. Instead, you could face unplanned downtime and asset failure, which greatly contribute to shorter asset lifetimes.
However, if you have asset information and data in a centralized database, you can effectively administer every asset you own throughout its lifecycle. You’ll have the data you need to maximize asset life, minimize the total cost of ownership (TCO) and grow your profits.
Why Do You Need EAM Software?
You need your assets to perform at optimal levels to reliably meet customer demand so why wouldn’t you use every tool at your disposal to ensure that your maintenance activities achieve those levels? An important feature of enterprise asset management software is the aforementioned asset lifecycle management.
EAM streamlines and centralizes the maintenance of physical assets throughout each asset’s lifecycle. If you rely on critical assets to meet production goals, you need an EAM.
Not only can you track and monitor your assets throughout their lifecycle, but you’ll also have accurate, real-time information about critical maintenance activities. A robust EAM gives you visibility into end-to-end maintenance management, from asset planning to disposal. With an EAM, you can also oversee labor and material resources, improve communications and keep operations running at peak capacity.
Next, we’ll discuss each of the four stages of asset management, how you can get the data you need throughout each stage and make intelligent decisions once your asset is ready for disposal and replacement.
1. Planning
In the planning stage, you are looking at acquiring a new asset. Maybe your old asset is outdated and not meeting safety or compliance regulations, or maybe it’s just not as efficient as it could be. Perhaps you have acquired new customers and you need to ramp up production. Or, you may be expanding your business to include additional product lines or product configurations.
Whatever the reasons, you need to know whether it is the right time to purchase a new asset and replace existing equipment. You’ll need to discuss options with stakeholders. Then you must conduct a review of the cost of acquisition, discuss the pros and cons of the asset from each available vendor, and finally, purchase the asset.
All this is contingent on having the right data.
If you’ve been tracking parts and service history, you should have the tools to see when and why equipment is failing more frequently and is therefore a candidate for replacement. This data can also inform the requirements for your new asset search, as failure analysis could indicate, for example, that you need more robust performance specifications around certain components of the asset. After all, if you don’t know what’s going on with your assets, it’s difficult to justify the expense of a new purchase.
How can EAM technology help?
In this case, you can view your maintenance costs along with historical trend data directly in your EAM system. You can drill down into the cost of each specific asset and even investigate which specific part keeps failing. With both custom KPIs and premade templates, Aptean EAM lets you generate a wide range of reports on asset performance. The EAM keeps track of the maintenance costs and historical trends of the asset throughout its life, so you have the information you need to calculate how much a replacement will cost your company.
Then, you can share the data with all stakeholders across your organization and streamline the decision-making process.
An EAM system can also help you track the planning phase. You can use Aptean EAM’s RFQ (Request for Quote) and procurement modules to execute the buying process. The project tracking feature of most EAMs allows you create a project plan for executing all of the phases of the planning phase with task execution workflows, task assignments and even time tracking and costs incurred during this phase. This history will be useful the next time you need to plan an asset buy or replacement.
2. Acquisition and Deployment
Once you’ve acquired the asset and added it to the factory floor, you need a way to keep track of it. While some enterprises have used paper files or spreadsheets to track this information, that is not the most efficient or accurate way to record such data. Regardless, make sure you capture as much detail about the asset as possible. For example:
Asset description
Serial number
Location of asset if you have more than one plant
Manufacturer and model
Date of purchase
Warranty details and expiration date
Equipment classification
Build the hierarchy and BOM for the asset
If you’re attempting to manage this information with paper files and spreadsheets, chances are some of this data will get misplaced. In addition, what if another branch needs the information? You’d have to stop what you’re doing, pull the file or look up the spreadsheet—assuming it’s up to date—and then call the other location back with the information.
As you buy parts and components, and begin to stock critical spares and replacement parts, these should be entered into your EAM software and tied to the hierarchy. Again, you can utilize the EAM procurement’s functionality to manage the process, and it will be easy to build this robustness out as you go as you input the information one time into the central database in your EAM for future usage.
Once set up is complete, you can use this information and maintenance data to schedule planned and preventive maintenance activities which can be conducted and processed quickly to avoid equipment downtime. You can also provide pertinent documents to maintenance workers for training and repair, calculate ROI of the asset and eventually inform the future repair vs. replacement decision of this asset.
3. Operation and Maintenance
The operation and maintenance stage will be the longest in the lifecycle of your asset—and at this stage is when an EAM really shines. The primary objective of an EAM system is to extend the life of your asset for as long as possible, while keeping costs to a minimum.
Modern EAM software is crucial for keeping physical assets in good operating condition. Using your EAM, the aforementioned planned maintenance schedules allow your team to perform the right maintenance on the right equipment at the right time. With excellent spare parts inventory management tools, you’ll keep inventory costs low and prevent stockouts to ensure quick and efficient repairs.
You’ll also be able to manage and track the performance of your assets over time—regular monitoring and maintenance of your assets is essential to detect any performance issues. With preventive maintenance schedules you reduce the risk of asset failures, reactive repairs and unplanned downtimes enabling you to gain increased uptimes and extend the useful life of the asset.
With an EAM system, you have a centralized data base to keep track of reports on callout outcomes, condition notes, user manuals, service logs and labor time spent. Additionally, the reporting and analytics tools in advanced EAM software allow you to see patterns in performance and conditions that might be problematic such as an increased frequency of breakdowns. At that point, you can create a report to ascertain whether the cost of maintaining the asset is more expensive than replacing it.
4. Asset Disposal
At some point, every asset you own simply becomes too inefficient to be profitable. This means that the operational costs to maintain it, and replacement parts, are greater than the cost of purchasing a new one. Maybe it has become obsolete, or perhaps it has broken down too many times. Bottomline, the asset has reached the end of its productivity and you need to dispose and replace it.
Your EAM is invaluable at this stage as well because you have been keeping track of your maintenance logs and have all records stored in one place, you can improve the equipment resale value if you choose to go that route. You have completed asset lifecycle management effectively and now you might be able to recoup some of the initial costs of the asset; assuming some value remains and because you have kept it in good working order.
While it’s never ideal to decommission and replace an asset, an aging asset can be a liability because it reduces production efficiency and increases safety risks. However, by tapping into the maintenance history, analytics and reports in the EAM, maintenance managers will have the data they need to make an intelligent decision about whether the asset should be repaired or replaced. A feat not easily accomplished with paper processes and spreadsheets.
Maximize Asset Value
Manufacturers are facing an uncertain future. Did you know that 70% of manufacturing companies don’t know when their equipment is due for maintenance? Moreover, costs are rising, labor shortages are plaguing the industry and one downtime incident can cost your company an average of $17,000. The problem isn’t the maintenance team—it’s the lack of data regarding the performance and condition of repaired assets. If you’re still using spreadsheets or manual processes, it’s likely that your maintenance operations are working on a reactive break-fix cycle.
Not only can this leave your business in the dust behind your tech-savvy competitors, but it can hurt your bottom line if you continue to incur superfluous and unplanned costs. Smart manufacturers make the most out of the resources and assets they have by using actionable data and automated maintenance schedules to prolong asset lifecycles.
Aptean EAM will empower you to maximize these assets by helping you manage every stage of the asset lifecycle management process. It will help optimize asset performance, reduce downtime, and improve efficiency and productivity while robust analytics will keep you on top of your maintenance metrics.
Not only that, but Aptean EAM has a team of dedicated professionals who understand the industry and will work with you through the life of the software—and beyond. Find out how, now.
¿Todo listo para transformar tu negocio?
Tenemos el software EAM especializado que necesita para conquistar los retos de su industria.
