What Is Industrial Internet of Things (IIoT) And Why Is It Important in Manufacturing?
What Is Industrial Internet of Things (IIoT) And Why Is It Important in Manufacturing?
What Is Industrial Internet of Things (IIoT) And Why Is It Important in Manufacturing?
Abr 14, 2020
Aptean Staff Writer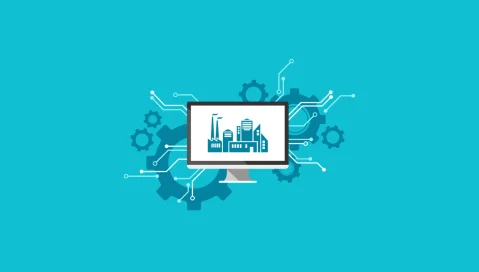
What Is IIoT?
The Industrial Internet of Things (IIoT) is the use of smart sensors and actuators to improve manufacturing and industrial processes. IIoT is an important part of what is described as the Fourth Industrial Revolution, or Industry 4.0. IIoT utilizes the power of smart machines and real-time analysis to take advantage of the data that machines have produced in industrial settings for years. The driver behind IIoT is that smart machines are not only better than people at capturing and analyzing data in real-time, but that they are also better at communicating important information faster and more accurately.
Connected sensors and actuators enable companies to detect inefficiencies and problems and to save time and money. The technology makes it possible to collect data for use in Business Intelligence (BI) and for Artificial Intelligence (AI). Within manufacturing, IIoT has great potential for follow-up and development of efficiency, quality control, sustainability, safety and traceability. In a manufacturing environment, IIoT is also the key to the development in predictable maintenance, zero-failure vision and improved efficiency in maintenance and service, energy management and asset tracking.
How Does IIoT Work?
IIoT is a network of intelligent devices, via networks linked to databases, which monitors, collects, exchanges and analyses data. Typically, an IIoT system consists of:
Intelligent equipment that can measure and store information about itself and communicate.
A data communication structure such as public internet or individual networks.
Intelligent applications that create useful information from raw data and utilize it to control and optimize processes.
Interface and analysis tools that provide people with the opportunity to utilize the information for qualified decision-making.
The connected equipment sends information directly to the IIoT infrastructure, where it is transformed into useful information on the status or performance of a machine, a group of machines or the whole plant. The information can then be used to optimize production and supply processes as well as foresee maintenance.
IIoT in Practice by Aptean
IIoT is described as a relatively new concept, but in fact the technology has been available and applied in different industries for a long time. Aptean has offered our customers the connection of machines and production equipment for more than 30 years. Using ordinary networks in the factory, or within whole groups of companies connected to a database, we have provided tools to create good decision-making for process improvement and preventative maintenance. Today, there are many more practical applications for the IIoT.
For many years, the easiest and most economical way to connect machines in an IIoT system has been to use a PLC device that is programmed to collect data on events, status and measurement values. Signals from the machines or from extra sensors and switches are used as inputs. The devices are easily connected to servers on site, or in the cloud via factory networks and the Internet.
An alternative method of connecting equipment that also has been available for a long time is to connect directly to the control systems in more advanced machines, via communication protocols like OPC-DA. The advantages of this connection method are a greater range of signals and that no additional hardware is required.
Aptean’s products today benefit from the more flexible OPC-UA and other modern standardized solutions, which creates the best conditions for a smooth and qualified connection of a large proportion of modern production equipment. Connection via PLC is a proven and cost-effective method that is critically important for older and simpler types of production equipment. Over the last few years, a plethora of IIoT units have also been developed that are designed to communicate directly with the outside world and so-called Edge units that function as an interface between a network of units and overall IIoT systems. With devices such as SICK TDC (Telematic Data Collector), Aptean can offer customers a simple and fast way to connect equipment without the need for access to the machines’ control systems or to the customers’ internal networks.
Important Base for Industry 4.0
Aptean offers its customers a complete solution for connecting all types of production equipment in all kinds of industrial production. With flexible solutions based on best practice and on modern technology, we quickly and easily connect equipment, collect data and make it available. The information creates direct value for customers who can optimize the utilization of their production equipment using our OEE and EAM solutions.
Our systems are built to be easily integrated with other IT-solutions and the collected data is thus available in other business systems such as MES, ERP and Supply Chain Management. Structured high-quality production information from Aptean’s systems is also a valuable data source for BI applications. By building from the ground up with production information and status in the production plant, Aptean Industry 4.0 Solutions are important building blocks in the development of the next generation of industrial production.
SaaS Solutions
All Aptean EAM and OEE products can be delivered as Software as a Service (SaaS).
Aptean SaaS and Aptean Industrial Manufacturing OEE or Aptean EAM API PRO Edition in the cloud, enables you to monitor your production, plan and execute your maintenance operations, as well as analyze your production and maintenance processes from anywhere at any time. Our cloud based products can easily be connected to production equipment and sensors for data collection using standard technologies such as OPC-UA, MQTT and web services like REST or SOAP. Aptean SaaS solutions offer a fast and flexible way to connect equipment and begin collecting data. Start measuring and building the foundation for your future manufacturing, today.
Want to learn more about how EAM or OEE solutions from Aptean can help your business? Contact us today to chat with one of our experts or schedule a demo.
¿Todo listo para transformar tu negocio?
Tenemos el software especializado en tu sector que ayudará a tu organización a prosperar.
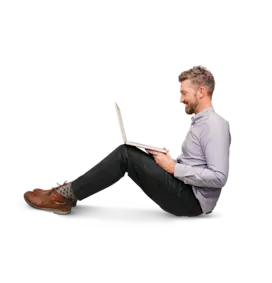