Aptean Apparel Shop Floor Control Case Study: Propper
Aptean Apparel Shop Floor Control Case Study: Propper
Aptean Apparel Shop Floor Control Case Study: Propper
Oct 15, 2021
Titular
- Propper Boosts Productivity With Real-Time Visibility Through Aptean Apparel Shop Floor Control
Established in 1967, Propper International is known for manufacturing the U.S. Navy’s iconic white sailor caps known as “Dixie cups.” As one of the largest official suppliers to the United States armed forces, the company, founded by William S. Propper, has manufactured over 60 million garments for the U.S. Department of Defense, Army, Air Force, Navy, Marines, Coast Guard and Special Forces.
Propper manufactures its boots, tops, bottoms, body armor, bags, pouches, accessories and sleep systems across six production facilities in Puerto Rico. The company also have manufacturing facilities in the Dominican Republic and Haiti.
The Challenge
Even with half a century of experience, Propper found itself facing a plateau in plant efficiency. Traditional processes for tracking work-in-progress (WIP) and piece-rate payroll had locked the company into a pattern in which unproductive time and manual procedures were taking a measurable toll every single day.
Even with multiple stations across its factories, inevitably lines would form, and the average associate might spend five minutes or more waiting for their turn to clock in
Operators spent about 15 minutes per day managing the bundle tickets and gum sheets to track an operator’s piece-rate production
The payroll department would then need to take all of this information, plus readings from the time-clock system, and manually scan and input the data in order to calculate payroll payments and generate production reports
“For practical purposes, we were almost always looking at information two to three days after the fact,” says Victor Acosta, Propper’s IT Lead for Business Analysis.
“It’s helping us be faster and more accurate with everything we’re doing right now. Instant feedback motivates workers to achieve higher performance levels.”
The Solution
The answer to eliminating a lot of this unproductive time and gleaning faster access to actionable information? Aptean Apparel Shop Floor Control (SFC) software.
This solution is designed to work entirely over Wi-Fi networks and standard, off-the-shelf tablets and Android™ mobile devices, and so Propper knew it would not need to add any hard-wired infrastructure to use it. Instead, the company installed about 850 mobile touchscreen tablets across workstations at its two factories in Puerto Rico.
Flat-screen monitors were also mounted on the walls of each factory, highly visible to all managers and employees. The mobile devices and screens are all connected to the SFC software which provides real-time visibility into productivity, order tracking, payroll, off-standard time and other metrics.
“The system has really paid for itself and is helping us be more responsive to our customers.”
The Results
Implementing Aptean’s specialized shop floor control software has led to double-digit efficiency gains for Propper and brought heightened operational visibility to both managers and production workers.
Gained access to actionable information faster, eliminating unproductive time
Enhanced managerial visibility into WIP across multiple sewing lines
Streamlined time tracking with QR code badges for operators and supervisors allowing them to “clock in” right at their workstation tablet
Sewing operator efficiency has improved by 15% on average since the SFC rollout
Propper team leaders now have increased visibility into individual efficiency and overall line performance, enabling them to offer constructive coaching and help associates improve their output and earn higher pay. In addition, associates and supervisors can handle off-standard events from their workstations, and managers can quickly identify any emerging bottlenecks with the real-time dashboards of WIP and order status.
Overall, Aptean Apparel SFC has given Propper much greater control over production management to increase productivity and performance.
Ready To Boost Productivity in Your Apparel Manufacturing Operation?
No matter what kind of fashion or apparel goods your business is producing, we’ve got the solutions you need to streamline operations, improve manufacturing productivity, gain end-to-end supply chain visibility, accelerate time to market and ultimately, boost profitability.
Sound good? Check out our apparel software solutions below or get in touch with our industry experts to request your personalized demo.
Learn more:
Related Content
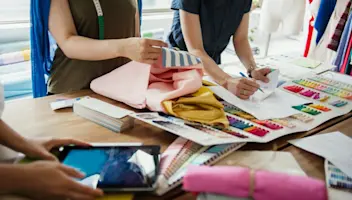

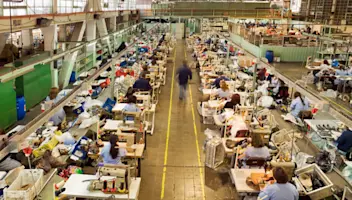
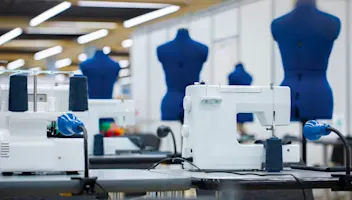
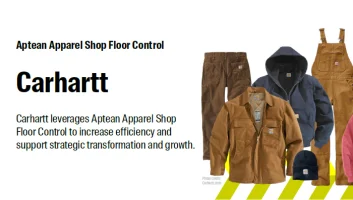
¿Todo listo para transformar tu negocio?
Tenemos las soluciones MES especializadas que necesitas para superar los desafíos de tu sector.
