Going Beyond FSMA Compliance: How Implementing an ERP System Can Add Value to Your Organization
Going Beyond FSMA Compliance: How Implementing an ERP System Can Add Value to Your Organization
Going Beyond FSMA Compliance: How Implementing an ERP System Can Add Value to Your Organization
25 Oct 2016
Jack Payne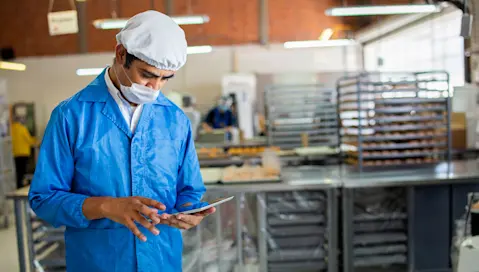
The Food Safety Modernization Act (FSMA) requires manufacturers and processors to evaluate and identify food safety hazards, implement preventive controls, and document those measures. Many companies see these regulations as a means of raising the bar for the food and beverage industry. It could be argued that standards are long overdue. Consumer confidence in food manufacturers is low. According to the 2016 Food and Health Survey conducted by the International Food Information Council (IFIC) Foundation, only 10% of respondents view manufacturers as trusted source for food safety.
More educated consumers combined with tougher industry standards are creating an environment where food manufacturers need to take additional steps to ensure their processes can meet these expectations. An ERP system specifically designed for food manufacturers will benefit a company as they comply with FSMA regulations regarding preventive controls, traceability, and documentation. Forward-thinking businesses are going even further, by exploiting the full capabilities of the system in order to improve efficiencies, reduce costs, increase margins, and increase customer service levels.
The Best Defense is a Good Offense
Prevention is the cornerstone of FSMA and is an important issue to consumers. Up to 15 million Americans have food allergies, and reactions can vary from a mild response, such as a rash, to anaphylaxis, which can be fatal. Undeclared allergens are the leading cause of recall. There were over 600 recalls in the United States and Canada in 2015, and a third of those were due to the same allergens: milk/dairy, peanuts, eggs, and wheat/gluten.
Food safety standards recognized by Global Food Safety Initiative (GFSI) are a good defense against potential recalls. When these certifications are complemented by intelligent technology, the protective net around the company tightens. For example, an ERP system with Allergen Control can prevent the creation of recipes containing allergens that are not allowed in the product being produced, as well as control material issues preventing ingredients to be added that are not declared on the label. In addition, using sequencing rules to manage when products with allergens are produced can help reduce any chance for cross contamination. As an additional benefit, improved sequencing using the planning and scheduling tools in ERP can also help reduce changeover times between jobs, thereby increasing utilization resulting in additional production capacity. Software can also capture and analyze data to identify where bottlenecks occur and allow managers to assess and correct such situations. What started as compliance with preventive controls became a more efficient production line, which can lead to greater revenue for the organization.
An Ounce of Prevention is Worth a Pound of Cure
The industry average cost of recalls is $10 million in direct costs, as well as brand damage and lost sales. Actual total loss data is seldom available, and the scope of the damage can be dependent on how well media attention and public perception is managed. Financial analysts estimate that Chipotle will have lost approximately three years of earnings between fiscal years 2014 and 2017, due to outbreaks of E. coli and norovirus. Additionally, they expect to spend about $50 million in food safety measures and marketing campaigns to regain consumer trust.
Hazard Analysis and Critical Control Point (HACCP) plans are the starting point in identifying vulnerabilities. By implementing a comprehensive track-and-trace solution, a company has the ability to conduct an efficient, targeted recall that minimizes potential harm to consumers and negative impact to manufacturers, distributors, and retailers. Using real-time data, problems can be quickly identified and drilled down to the exact culprit within the supply chain, thus avoiding mass recalls. Mock recalls utilizing a robust traceability system reduces the timeframe to execute a recall from days to minutes. Fewer recalls improve bottom line performance; recovery expenses are avoided, the company brand is protected, and supplier relationships are preserved.
Don’t Get Lost in Translation
FSMA regulations require much more stringent data management procedures; there are guidelines as to what data must be recorded, how to record it, when it must be recorded, and which employee recorded it. Standalone applications and homegrown measures can be time-consuming as information is keyed into multiple systems, and the probability of inaccurate information increases due to errors in reentering data. Comprehensive reporting also becomes difficult as information has to be pulled from various systems and compiled in another.
A fully integrated ERP system provides a single source of truth. It should be powerful enough to capture detailed data and flexible enough to produce reports suitable for an auditor. Errors decrease and quality increases when employees have access to documented processes. Business intelligence and analytic solutions present Key Performance Indicators (KPIs) that make it easier to identify situations that require attention. Drill-down capabilities enable users to identify trends and conduct root cause analysis. Real-time information is available to support manufacturing and distribution activities. Managers can focus on strategic planning rather than time-consuming administrative tasks.
Conclusion
FSMA will have some kind of impact on almost every food manufacturer moving forward and into the future. While compliance is mandated, there can be additional benefits for those organizations that choose to go beyond the minimum standards. A comprehensive ERP system allows a manufacturer more in-depth information about their operation. Such a view allows for improved inventory management as resources are better utilized; increased customer service levels as more accurate electronic records are used in forecasting and planning; and increased efficiencies as workflows are simplified and the possibility of human error is minimized. The end result is a more productive, more profitable organization that has earned the trust of its customers and the confidence of consumers.
Food Insights
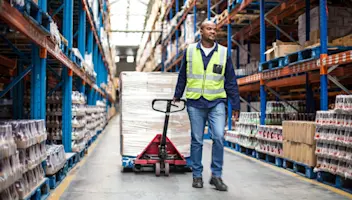
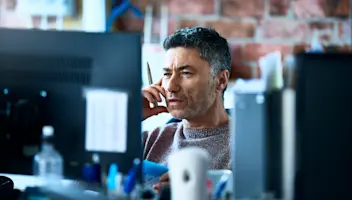
¿Todo listo para transformar tu negocio?
Tenemos las soluciones ERP especializadas que necesitas para superar los desafíos de tu sector.
