Leadership, Training and Processes Key to Aptean TabWare EAM Implementation at UFPI
Leadership, Training and Processes Key to Aptean TabWare EAM Implementation at UFPI
Leadership, Training and Processes Key to Aptean TabWare EAM Implementation at UFPI
9 Mai 2018
Kay Jenkins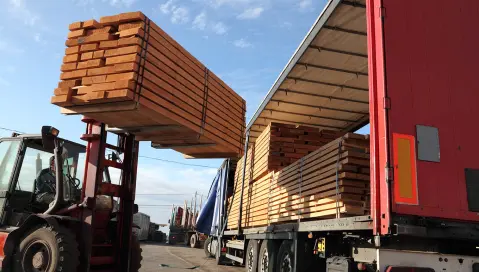
Getting a company with 130 independent locations up and running on a CMMS/EAM system sounds daunting. However, recent implementations by Universal Forest Products across its large, distributed organization prove it can be done. The keys: dedicated leadership, effective training, and standard processes.
Universal Forest Products (UFPI) is a leading manufacturer and distributor of engineered wood and construction materials in the retail, industrial, and construction markets. Initially, only one of the 130 UFPI plants had a CMMS/EAM system, and a few locations used paper work orders. Most had no solution in place at all.
The lack of a formalized preventive maintenance system was affecting productivity in the plants, with unexpected breakdowns causing costly repairs and overtime expenses. With more sophisticated equipment being introduced in UFPI plants, it became vital that it be maintained to the manufacturers’ recommendations to preserve warranties and realize expected increases in productivity.
Executive support for a solution led to the selection of Aptean TabWare EAM due to its full features with standard processes and workflows, ease of use, and total cost of ownership. Implementation began, and so did learnings about how best to plan and manage such an effort in a large number of independent locations. They included:
Establish a dedicated maintenance system lead. Even though the project had executive support, convincing plant management of the benefits of a CMMS/EAM system was a challenge. The company originally planned for regional engineers to be responsible for TabWare implementation at their facilities; however, it became apparent that solution wasn’t practical, given the engineers’ regular responsibilities.
Instead, the company established a dedicated maintenance system lead as a single point of contact to streamline TabWare implementation and user training. One individual with the appropriate skill set made the implementation easier to plan, schedule, and support.
Focus training on specific user roles. UFPI’s approach to TabWare training and support has led to almost 100% user adoption. The company believes that the best way for employees to embrace TabWare as their own is to have skin in the game as early as possible. To that end, the EAM system lead examined what each user persona would be doing within the system to focus training on specific responsibilities, with scenarios presented in the training environment that mimic each role. New users then enter actual work orders into the live system to reinforce learning.
In addition, the company created a workflow process and training videos for maintenance supervisors, and provides general managers at each location with an overview document that details the benefits of using TabWare.
Create standard processes. Currently, 28 UFPI facilities have implemented TabWare, and the goal is to add eight locations per year. In an organization as large and distributed as UFPI, implementation time for TabWare varies from site to site. To help, the maintenance system lead developed a standard, repeatable process for data migration, training, and support. UFPI also uses TabWare’s cloud model, which allows for rapid deployment. As a result, TabWare generally has been live at UFPI sites within three weeks.
UFPI’s initial TabWare implementations have proven to be a success. Early adopters of TabWare expressed satisfaction with the system, and demand among other facilities began to grow. Facilities have seen fewer breakdown work orders as a result of the shift in maintenance strategy. For example, one of the larger plants at UFPI demonstrated the power of TabWare combined with a disciplined maintenance program by reducing breakdown work orders by 30%. Improvements made at each location have validated UFPI’s investment in and approach to implementing our comprehensive enterprise asset management solution, Aptean TabWare EAM.
To learn more about how UFPI uses TabWare to improve its operations and effectiveness, read this recent case study.
Related Content
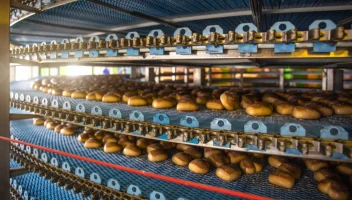
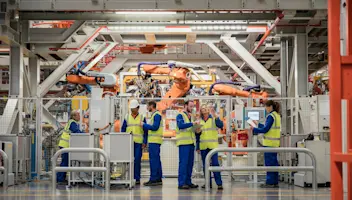
Commencez à transformer votre entreprise dès aujourd'hui
Prêt à faire passer votre entreprise à la vitesse supérieure ? Nous sommes là pour vous.
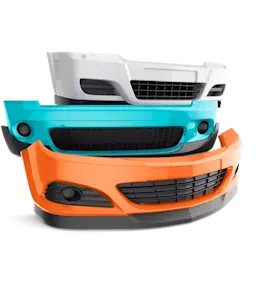