4 Ways That Implementing Chemical ERP Software Improves Your Operations
4 Ways That Implementing Chemical ERP Software Improves Your Operations
4 Ways That Implementing Chemical ERP Software Improves Your Operations
16 Apr 2021
Daniel Erickson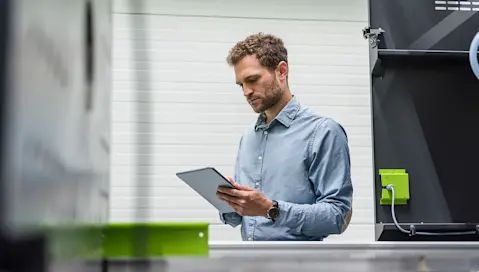
Even before the global pandemic, the chemical manufacturing industry was under pressure. Political and economic uncertainties, pricing pressures and the challenges associated with managing demand created a compelling case for a strategic rethink. COVID-19 sealed the deal.
As we emerge from 12 of the most turbulent months in modern history into a period of stabilization and growth, smart manufacturers realize that something needs to change. That a more robust operational approach is needed to survive – and thrive – amid market turbulence.
The good news is that this resilience can be delivered through manufacturing technology. And the right software will give you greater agility to pursue new market opportunities.
Want to know more? Here are four ways that implementing a chemical enterprise resource planning (ERP) solution will improve your operations:
1. Greater Inventory Visibility
While the multichannel environment generates new opportunities for growth, it also increases the potential for siloed working. To build a resilient manufacturing operation, you need to facilitate collaboration across channels—between people, processes and data.
Investing in chemical ERP software will enable your organization to do all three, by centralizing the databases that your workforce are using. This way, everyone has access to the same, real-time information, and can understand the impact of their decisions on other parts of the business.
With the right ERP software in place, every team can work harmoniously. For example, your production floor and purchasing department will be able to integrate work in progress (WIP) and finished goods information with inventory levels – including raw materials and packaging – to optimize schedules.
2. Streamlined Regulatory Compliance
If multichannel operations aren’t complex enough, chemical manufacturers are also dealing with a host of government and regulatory body requirements.
These compliance demands can take the time and focus away from production—particularly when legislation and best practice are continually changing. For example, this February, the Occupational Safety and Health Administration (OHSA) proposed amendments to how chemical products are labelled in the workplace, in line with updates to the United Nations’ Globally Harmonized System of Classification (GHS).
The latest changes include creating a new hazard class for desensitized explosives, which may affect manufacturers, importers and suppliers of aerosol products and flammable gases. Information will also need to be reported to downstream workers and users as part of existing GHS protocol.
Chemical ERP software can help to manage the compliance burden placed on your manufacturing business, by integrating reporting for GHS requirements and automatically creating Safety Data Sheets within the system. A good ERP platform will also be able to store documentation centrally in the cloud, for both internal staff and outside agencies to access in order to manage industry audits.
3. Innovation in the Supply Chain
The global chemicals industry is extremely vulnerable to fluctuations in commodity pricing, so you need to be smart about how you buy raw materials in order to remain competitive. This means sourcing the right ingredients at the right time to keep production flowing, from a supplier that is offering a reasonable market price.
Chemical ERP technology can support your operation here, as it gives you immediate insight into upcoming demand. The right software will enable you to map your schedule against current inventory levels – along with any supplier lag times – to optimize speed of production.
More importantly, a dynamic chemical ERP solution will give you the flexibility to pivot operations as things change—from reacting to shipping delays, to sourcing from an alternative supplier if your current vendor has no availability.
4. Enhanced Product Recall Processes
In an ideal world, improving your operational approach would mean product recalls never occur again. But even with greater accuracy and accountability, things happen that are beyond your control.
The only thing you can do is react quickly. And if your ERP technology has full forward and backward lot tracking functionality, you will be able to easily locate any production batches that could contain a recalled product.
Locating and quarantining contaminated goods that haven’t yet left your warehouse, and getting in touch with external parties to recall affected batches, is the most effective way to limit potential damage. Your number one goal is to launch a rapid response, so contaminated products are isolated and destroyed before they reach the end customer.
Building a Robust, Flexible, Future-Forward Business
While every sector is striving for recovery and growth post-COVID-19, chemical manufacturing needs a robust, flexible operation more than other industries. Your business will face continual challenges from external market influences: international trade relationships, supply chain delays, climate change commitments, political sensitivities and evolving policies. How you respond to these forces will determine your long-term success.
Chemical ERP software is a critical tool for enhancing your manufacturing operation, as it gives you the cohesive, data-driven platform your business needs to make informed decisions. And it also provides the agility to react to what’s happening in the wider world—either seizing new opportunities, or limiting damage.
We will never be able to control the world around us, but this shouldn’t be a source of fear. Running an efficient, responsive operation through ERP software drives profitability from the inside-out. And it also gives you the agile, scalable tools needed to pursue growth opportunities—pushing your chemical manufacturing business forward into the future.
Our purpose-built process manufacturing ERP, Aptean Process Manufacturing ERP, has been developed for manufacturers in the specialty chemical industry. The solution solves the critical needs and sustainability trends for process manufacturers, including lot tracking and formula management.
Schedule a personal tour of Aptean Process Manufacturing ERP and see how its core chemical manufacturing functionality and advanced features can get to work for you right away to improve your operations.
Bent u klaar om uw bedrijf radicaal te veranderen?
We hebben gespecialiseerde ERP-oplossingen waarmee u elke uitdaging in uw branche aankunt.
