The Circle of Engagement
The Circle of Engagement
The Circle of Engagement
30 Jun 2016
James Wood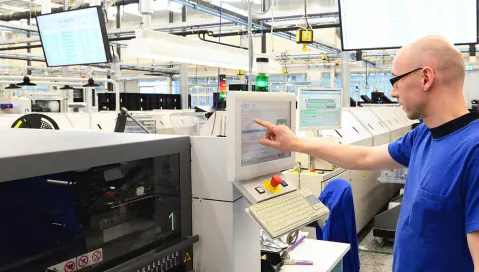
For any manufacturing organization, achieving the highest levels of operational excellence is built upon the engagement of its employees. Employees are expected to be active in collecting information, surfacing and resolving problems, and recommending improvements that could be made as a result.
Unfortunately, all too often their insight is not acted upon, and the impact on factory-floor morale is considerable. They feel like they are simply doing it “for the sake of doing it.” When an employee feels that the tasks they are being asked to do have no positive impact on them and the way they work, they almost immediately become disengaged with the entire process.
They might feel that their voice is not being heard or, in the worst case, that the feedback and data they are providing is not trusted by their superiors. That, in essence, indicates to them that their professional integrity is being questioned, and they are not truly valued, rather they are simply a workhorse whose intellectual contribution is effectively irrelevant.
This is the worst use of people, the strongest asset companies have available. These are the people who have the benefit of years of experience; they understand the issues, and it is of utmost importance that their innate knowledge is collected as data, transformed into information, and converted into the knowledge that a company needs to improve operational efficiency.
Finding a means to engage your people on a company-wide basis is the route to achieving this.
The Tools to Perform
By giving operators a simple, unobtrusive tool that makes their working life easier, it becomes very straightforward to enter their knowledge and experience into the company's system. But not only that, it should be a sophisticated, intelligent tool that allows this feedback to be presented in real-time, meaning it can be acted upon immediately, and employees can see that their input is being used and is trusted.
This real-time element is key. Waiting until a shift has ended is too late to analyze performance and quite often, valuable insight gets lost among the noise. This gives the impression to the employees that the company is 'driving in the rear view mirror'- without focused direction, missing the factors that can keep a business on track.
The ability to review the data, both in real-time and at key intervals during the shift, means action can be initiated to ensure inefficiencies are removed from the process in-flight. By performing these frequent reviews, operators see that their input is being used to drive continuous improvement. They feel trusted. They feel engaged. They feel motivated to continuing to perform to the highest standards, not just for their own sake, but for the sake of the team. Quite simply, they won't see any reason to consider leaving, which of course has its own business benefits in terms of preventing high staff turnover and the associated costs of employee churn.
Furthermore, satisfaction and pride in their employment will inevitably lead to them vocalizing this outside of the workplace- to their family and friends, or to potential customers and even prospective employees.
Developing a coherent, lasting working relationship- from the upper management through to each individual contributor- will only service the company well in the future.
Good Data In Equals Good Data Out
Of course, realizing this operational nirvana is dependent on the quality of the data and the system being used to capture it, and on how this system is integrated into day-to-day operations.
That means collaborating with a software partner that not only installs and implements the software, drawing upon years of experience of successful projects in the specific business vertical, but implements a system aligned to common manufacturing metrics. At the same time taking care to balance the organization's needs and its working culture, to ensure high awareness and engagement so employees can execute their roles in the most productive manner. Factory-floor employees are the ones who can identify the biggest, most frequent pain points that need resolving. Then, the solution can be tailored to match, and thus, built to make positive gains in the key areas.
A business might have a problem with a wasted product, a culture of costly overtime, or an issue with machines not being optimized to their full capacity. There are so many factors that impact operational efficiency that, if neglected, impact employee engagement. It may surprise you how quickly an effective manufacturing execution system will deliver a return on investment - not only in terms of efficiency gains and your company's bottom-line - but in the overall happiness of employees.
Full-Circle
Having insight into manufacturing inefficiencies means businesses can be more agile in production and allows them to continue to meet production demands and growth targets in a structured, manageable way. A way that says to the employee, 'you are what makes this business work'- from the operators, to line managers, to data analysts. Once the stream of data flows into a sea of knowledge, the strategic decision makers will be better placed to identify historic trends, build analysis and make changes for the better.
Quality data and a quality system to capture it are the keys to driving a collective culture to never stop improving. Only by recognizing and acting upon employee input can the circle of engagement be complete.
Learn now, how with Aptean, contact us today.
Gerelateerde inhoud
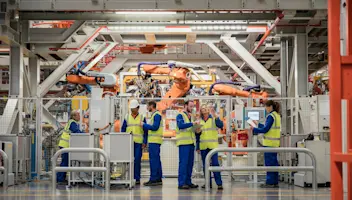

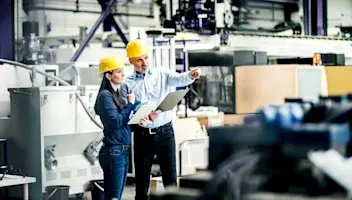

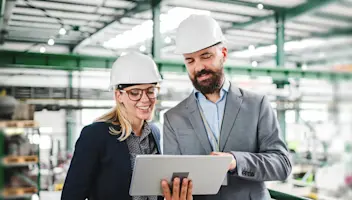
Zet vandaag nog de transformatie van uw bedrijf in gang
Bent u klaar om uw industriële productie naar een hoger niveau te tillen? Dan helpen we u graag.
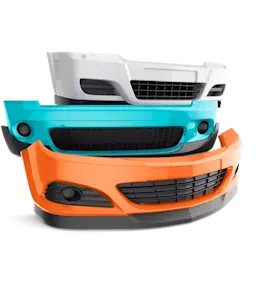