Aptean Agility CMMS Case Study: Wienerberger
Aptean Agility CMMS Case Study: Wienerberger
Aptean Agility CMMS Case Study: Wienerberger
4 Nov 2024
Aptean Staff WriterBlog Post
- Revitalising our systems usage to further enhance our operations, maintenance, and estate management.
Background
Founded in 1884 in Africa, PZ Cussons operates internationally as a supplier of consumer goods that champion the wellbeing of people, families, and communities everywhere. With their UK headquarters based in Manchester, PZ Cussons Ltd is a leading British manufacturer of personal healthcare products and consumer goods including brands like Carex, Imperial Leather, Sanctury Spa, and St. Tropez.
PZ Cussons adopted Agility CMMS in 2015 as part of their maintenance strategy to centralise their schedules and jobs and remove the need for paper documentation. Since then, various team members have been involved with the system and in more recent years, the Head of Engineering, Simon Breheny, and Engineering Leader/Maintenance Planner, Marc Bull, have been ensuring effective maintenance planning and management with Agility CMMS.
The Solution
Agility CMMS was selected to centralise all maintenance and help the organisation with their sustainability efforts in terms of using less paper. They manage several work order types including:
Annual site wide shut down – carried out once a year for bigger maintenance tasks.
Workshop repairs – equipment that might sit on a shelf for example and not be used all the time, but the team can pick these up as and when they have availability.
Urgent repairs / Breakdowns – utilising the Agility helpdesk jobs are logged with the support of triage questions which help assess the issue. These jobs are then crowdsourced and sent directly to the team to pick up urgently.
Corrective jobs – these are less urgent and sit in a backlog, they’re dealt with daily through the engineering planning meeting.
Facilities corrective jobs – directly related to the building rather than machinery or equipment, these jobs are managed with the support of the facilities team.
Improvement jobs – these are assessed daily through the site improvement engineer who then prioritises the jobs based on risk and cost.
As Simon shared: “With Agility CMMS everyone is more organised, and we can manage our jobs more effectively. Different jobs go to different people based on their skillset, but everyone can see what they have to work on with a task list. We can also see who has what on and how quickly the team are getting through the jobs, supporting us to manage our resources. We can effectively monitor the progress of jobs, and we can also see if jobs are being passed back to others for support, enabling us to work as a team to complete all the jobs. It also lets us allocate for interventions which we can do daily.”
Marc went on to describe: “We have dashboards around the business providing transparency as to where we are with maintenance jobs, what needs to be done, and what we have achieved. There is a screen in reception, so it is the first thing everyone sees when they come in, and it updates in 30 second intervals, displaying Work Orders, breakdowns, and more.”
Simon continued: “Agility allows us to prioritise jobs which helps us to continuously improve our response times. It might be that we have a month to complete a job as it is non-urgent, or 7-days, or 24hrs, this steer enables us to support production and be on the case with urgent jobs as quickly as possible to help avoid downtime.
All our planned maintenance is allocated with a month priority and scheduled in for the month, sometimes these get pushed and cross over into the next month. However, the Agility dashboards allow us to see where we are in terms of compliance so we can bring things forward if needed, to ensure we are always on top of it. We track all our statutory planned maintenance so things related to fire like pumps, etc., and these are carried out in weekly fire risk assessments, and we can easily pull up reports on these at any time.”
Marc followed by saying: “We can see the number of open Work Orders (WO), how many are raised in a week, and we can then allocate these to those we can see might have spare time. Everything is in Agility, everything in terms of our maintenance planning waits in Agility for the team to action it.”
Simon went onto talk about production: “Here at PZ, we don’t keep much stock on site, we have four-hour deliveries including bottles and caps, and all the teams work on a shift basis. For maintenance and production, shift teams’ management can see what everyone is doing and where any problem or impact areas might be. Handovers between shift teams used to be a massive issue with sign off sheets and taking tools off, and things, but we don’t have this issue with Agility, it gives everyone transparency.
As a team we can forward project what is coming up, it’s all in Agility, so we can think about whether we need to pull things forward or if we need to think about additional resources. It is massively helpful in terms of not just managing jobs, but also managing our labour resources.
Dashboards have made a massive difference, and the reports are great, and give us all sorts of information. For example, we have a due date performance report – we can see if a due date has been moved, did you complete it on time, or move it. Maintenance efficiency can be measured so things like we can see over 95% of scheduled jobs were completed on time. We’ve got instant visibility of outstanding PMs, and we are really pleased that we’ve been compliant with our PMs for over 4 months now which is great. Everything the engineers do is in one place and can be accessed in terms of compliance and audit data. Our completed jobs have gone through the roof, and it is a really positive stat to display on the screens around the site.
Every engineer now has a challenge to raise 10 WOs per month off a PM or a breakdown or as they are walking around. They can scan the QR code we’ve placed on all machinery and log it quickly, and it means we’re monitoring everything closely.
We have evolved our use of the system over the last 6-12months, and Agility makes life so much easier for everyone from the guys doing the jobs to us planning and managing maintenance, to reporting elsewhere in the business as to how we’re doing.”
Marc went onto mention logging jobs: “We have allocated an iPad to each line so it’s quick and easy to login to Agility and raise a request. The triage questions make it quick and simple for a job to be logged, and then it can be automatically allocated to the engineers to work telling them if it is a breakdown, corrective, improvement, or automation. Agility supports us to be more efficient and makes it so much easier for everyone to manage maintenance jobs, supporting us to ensure production lines are up and running.”
The Future
Looking to what next for the future, Simon explained: “The more we use Agility, the more we can see what it has to offer. The user day was good, and we heard what other users were doing, and we like the monthly webinars.
We now have a standard completion report with fault groups and the fault call they relate to. Once we have some more data here, we will be able to identify any ongoing issues like why does line 3 have a continual fault.
We have also made a checklist that can be signed by a shift authorised person on the DRA for things like working at height permit, this goes live next month, and not only speeds up the process but also gets ride of more paper and helps with our sustainability goals.
In addition, we are looking at how we use the Agility inventory functionality more as we know we can integrate it with SAP, and this is something PZ I.T. have agreed we can pick up next year.”
Marc concluded: “We are looking forward to further working with the SSG Insight team, our Account Manager is really good and stays in contact with us regularly, the Support guys are always on the case if we have an issue, and we’ve enjoyed working with the Consultants who are really knowledgeable.”
To find out more about how we work with PZ Cussons and other manufacturers around the world, please contact a member of our global team today.
The Solution
Agility was first introduced to Wienerberger UK in 2016 and usage of the solution has grown to 14 sites with:
7500 Assets Listed
4055 PPMs (Preventative Planned Maintenance)
Over 320 user accounts 70% of which have Agility Mobile
“Once we introduced Agility, we were able to start gathering our data in a more consistent and cohesive way and we were able to better manage our asset maintenance timetable
Agility is designed for many different businesses across lots of different sectors however, it is not rigid, and we didn’t have to change lots of our processes to fit Agility, Agility was and is flexible enough to meet with our specific requirements.
I can see everything from the Work Order List to the Equipment Structure, to Job Analysis (completion, open, etc.), to Labour Utilisation, Priority Codes, Shift Logs, Checklists, and more. The way Agility has pulled all this information together for us and centralized it is now vital to our business and makes life so much easier when it comes to reporting.
We have checklists on all our PPMs to simplify our maintenance, we’ve introduced mobile phones so that the team can access these on the go and have all the information they need to get the job done. It also means they can complete a job there and then with any comments and photographs, so it makes the whole process far quicker than them having to complete the admin later. It also means we have realistic timescales as to how quickly jobs are being completed.
We have integrated a Criticality Factor based on the Failure Mode, Effects and Critical Analysis (FMECA) matrix from the PIP+ guidance. In addition, we’ve also created QR codes using FLOC (Functional LOCation) numbers, and we’re integrating Meerkat Continuous Monitoring sensors through the custom API.
If I had to describe using Agility in a nutshell, for me, it is pivotal that all our data is in one place and that we have visibility of the reports. Things like maintenance time control, job completion by job type, outstanding work orders by priority and by overdue timescale, jobs raised, jobs by craft, and of course maintenance against our KPIs. It’s all there in visual dashboards that I can easily share with others so that we can all understand what’s going on.
The team at SSG Insight have supported us throughout and I love the way the team are always looking at new things for the software and new technologies to integrate with. There’s lots of innovation, and we’re involved in that process. The team often visit to see how we are, but also to see the Agility solution in action and understand exactly how we’re using it, why we do things a certain way, and more. They try to work with us to help us maximise our use of the software and to ensure that they are evolving the solution to meet our future needs.
The support team are quick to reply and respond, which is helpful. Any of our users can access support as and when they need it, and then we share the responses across our teams in case it’s of use to them too. Plus, if it’s something that needs to go to development, the SSG Insight team escalate it, but they keep you informed the whole time.
Don’t get me wrong, not every solution is perfect, but they take the challenges and problems we have as a business and try to help us find ways to solve them with Agility. Relationships wise, the team do a really good job. We work closely with our account manager, but we know the team in product, support, the tech consultants, and many others, as well.
In addition to the SSG Insight team visiting our sites, we’ve been on some training and have found the courses useful. We also like the complimentary monthly webinars which showcase different aspects of the software. Sometimes it’s something we’re already using, sometimes it’s not, but it always sheds light on something we didn’t know which is great and helps us to utilize the solution more effectively.
Training and the webinars, help to bring together our teams across the different sites. All the sites are on an Agility journey, but they’re not all quite at the same stage. However, bringing all our systems together under one umbrella with a centralised view across our sites has made a massive difference for our business.
"There is now detailed data behind every single asset. Everything is aligned, everything is there, and our reporting is now far easier as we have that comprehensive visibility which we lacked before Agility."
The Future
Looking to what next for the future, Simon explained: “The more we use Agility, the more we can see what it has to offer. The user day was good, and we heard what other users were doing, and we like the monthly webinars.
We now have a standard completion report with fault groups and the fault call they relate to. Once we have some more data here, we will be able to identify any ongoing issues like why does line 3 have a continual fault.
We have also made a checklist that can be signed by a shift authorised person on the DRA for things like working at height permit, this goes live next month, and not only speeds up the process but also gets ride of more paper and helps with our sustainability goals.
In addition, we are looking at how we use the Agility inventory functionality more as we know we can integrate it with SAP, and this is something PZ I.T. have agreed we can pick up next year.”
Marc concluded: “We are looking forward to further working with the SSG Insight team, our Account Manager is really good and stays in contact with us regularly, the Support guys are always on the case if we have an issue, and we’ve enjoyed working with the Consultants who are really knowledgeable.”
To find out more about how we work with PZ Cussons and other manufacturers around the world, please contact a member of our global team today.
"There is now detailed data behind every single asset. Everything is aligned, everything is there, and our reporting is now far easier as we have that comprehensive visibility which we lacked before Agility."
Ali Ben Henda, Continuous Improvement Manager
Related Content
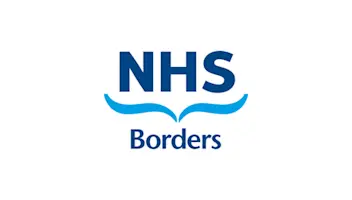

Ready to start transforming your business?
We’ve got the specialised EAM solutions you need to conquer your industry challenges.
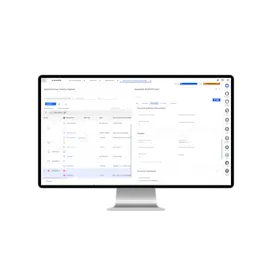