The Top 6 Benefits of a Mixed-Mode Manufacturing ERP
The Top 6 Benefits of a Mixed-Mode Manufacturing ERP
The Top 6 Benefits of a Mixed-Mode Manufacturing ERP
Mar 20, 2025
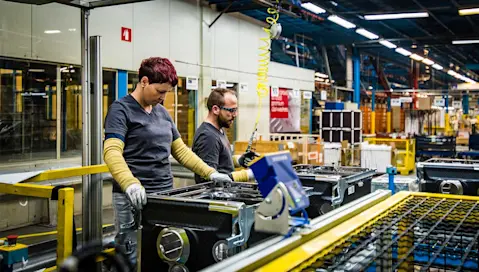
If you’re running a mixed-mode manufacturing operation, you're no stranger to the constant balancing act. One day, you’re producing make-to-stock goods to keep inventory levels steady. The next, you’re managing a rush of make-to-order jobs, each with its own unique specs and deadlines. And let’s not forget the rising material costs, changing regulations and the never-ending need for speed and customization.
Sound familiar? Then you also know that trying to manage all of this with generic software—or worse, outdated or manual systems—just adds to the chaos. You don’t need another workaround. You need a system that’s actually designed for the way you operate.
That’s where a mixed-mode enterprise resource planning (ERP) comes in. Designed for manufacturers like you, it brings everything together—production planning, inventory management, compliance and more—giving you the power to run a smooth, efficient operation and regain control, instead of constantly putting out fires.
In this blog, we’ll break down the biggest benefits of a mixed-mode manufacturing ERP and how it can help you take control of your operations. But first, let’s break down exactly what kind of businesses this specialized manufacturing software can enhance.
What Is Mixed-Mode Manufacturing?
The term mixed mode-manufacturing can apply to many types of businesses, across various industries, but they all have one commonality: they use more than one production method. Most often it refers to the blend of make-to-stock (MTS) and make-to-order (MTO) strategies within one operation, but in some cases can also cover manufacturers that straddle both the discrete and process manufacturing worlds.
Let’s break this down.
Make-to-stock is all about efficiency and scale. You produce goods in anticipation of demand, filling shelves or warehouses with ready-made products. For example, a furniture manufacturer might produce hundreds of identical dining tables to meet forecasted demand at retail stores.
On the flip side, make-to-order, make-to-engineer (MTE) and job shops are about customization and flexibility. You start production only after receiving a specific customer order. Imagine the same furniture maker crafting a one-of-a-kind table designed to fit a customer’s unique style and space requirements.
Combining both methods in a dual approach allows businesses to meet broad market demands while staying agile enough to capture niche opportunities. Here are just a few examples of the types of operations that can capitalize:
Apparel Brands: Producing staple clothing items like t-shirts and jeans for mass retail while offering bespoke tailoring or limited-edition designs.
Food Producers: Packaging ready-to-eat meals for supermarkets while crafting specialty products like customized wedding cakes or private-label sauces.
Tech Companies: Manufacturing standard laptops for retail shelves while building custom configurations for businesses.
So, whether you’re crafting high-end furniture, bottling craft beverages or assembling tech gadgets, mixed-mode manufacturing could be the key to staying competitive. And choosing a specialized ERP for manufacturing is your path to achieving it efficiently.
6 Key Benefits of a Mixed-Mode Manufacturing ERP
Managing both make-to-stock and make-to-order production within a single business model brings a unique set of challenges. It’s like juggling two balls of different sizes—keeping them both in the air requires precision, flexibility and a good bit of strategy. That’s where you need an industry-specific ERP system. Thankfully, specialized mixed mode manufacturing ERP software provides many useful benefits to help with the specific complexities of your environment.
1. Greater Flexibility and Productivity in Planning and Scheduling
Do these scenarios sound familiar? A customer suddenly changes their order, your supplier is running late, or you need to prioritize a make-to-order job over a make-to-stock run with short notice. In a mixed-mode environment, these shifts happen all the time—and you can’t afford production delays.
A mixed-mode manufacturing ERP gives you the flexibility and control to adjust on the fly—keeping you ahead of planning and scheduling challenges and ensuring production runs smoothly. Here’s how:
AI-powered demand forecasting: Say goodbye to stockouts and overproduction. A mixed-mode manufacturing ERP can provide data-driven insights to help you forecast demand trends so you can plan smarter—not just react.
Dynamic real-time scheduling: A mixed-mode ERP doesn’t just create a schedule and then move on—it can pivot easily when priorities shift based on real-time order, capacity and material data. This sophisticated automation means you can minimize late jobs while maximizing throughput.
Capacity planning to prevent bottlenecks: No more overloaded workstations while other machines sit idle. An ERP for mixed-mode manufacturers balances workloads across different production types, keeping production and fulfillment on track.
2. Improved Efficiency With Streamlined and Integrated Operations
Disconnected systems? Manual data entry? A constant back-and-forth between departments? All of these things are productivity killers. But a mixed-mode ERP eliminates these inefficiencies by integrating every part of your operation—from production and inventory management to finance and customer orders. Here’s how a mixed-mode manufacturing ERP improves data accuracy and streamlines workflows across your organization:
End-to-end visibility: With real-time dashboards, you can see production status, inventory levels and work orders at a glance—there are no more blind spots even as you switch between modes.
Automated workflows that cut out manual tasks: A sophisticated AI-enhanced ERP system can automate a range of time-consuming or repetitive tasks. From auto-generating work orders to tracking materials, you spend less time fixing errors and more time getting things done.
Seamless collaboration between teams: No more chasing down information. With one fully integrated and centralized system, your engineering, sales and production teams work from the same, up-to-date data, eliminating miscommunication and boosting productivity.
3. Enhanced Compliance and Quality Assurance
Let’s be real: manually managing compliance is a nightmare. And it only gets worse as you manage different modes and production processes that fall under different regulations. But, keeping up with legislation is non-negotiable so making it as painless as possible should be a top priority.
Here’s how an ERP for mixed-mode manufacturing keeps you audit-ready 24/7:
Full traceability and tracking: Need to trace a batch back to its raw materials? No problem. Need a digital audit trail for every step of assembly? You got it. A mixed-mode manufacturing ERP tracks every component from start to finish without extra paperwork.
In-process quality inspections: Catch defects before they become a problem with automated quality control checks built into your workflow. So not only are you confident your regulatory compliance is up to scratch, but you can rest assured consistency for your customers is taken care of, too.
Instant document and report access: With a purpose-built mixed-mode manufacturing ERP you can generate certifications, compliance documents and audit reports in seconds—not hours.
4. Smarter Inventory and Supply Chain Management
One of the biggest challenges in mixed-mode manufacturing is keeping the right materials in stock without overloading your warehouse or facing last-minute shortages. Imagine the relief of not having to worry about excess stock or costly production delays. This is the peace of mind that comes with a well-optimized inventory and supply chain.
Let’s look at how a mixed-mode ERP keeps your supply chain lean and agile:
Live inventory tracking: With detailed, real-time lot and item tracking, you know exactly what’s in stock, on order and in production—at any moment. So, you can ensure orders stay on track for on-time, in-full delivery.
Automated material planning: A mixed-mode manufacturing system calculates material needs based on real-time demand—so you are never over- or under-stock.
Supplier performance monitoring: To ensure a streamlined supply chain with no unexpected delays, you can track vendor reliability and lead times to avoid disruptions.
5. Faster, More Reliable Order Fulfillment
Whether they’re waiting for bulk deliveries of make-to-stock orders or smaller runs of customized products, your customers expect speed, accuracy and flexibility. If you can’t deliver, it will affect your business and brand value. Therefore, you need a manufacturing ERP that helps you fulfill orders faster and more accurately.
So, how does a mixed-mode ERP help you deliver on time, every time?
Real-time order tracking: With the organization wide visibility and integration of a mixed-mode manufacturing ERP, sales, production and customers can see exactly where an order stands—reducing follow-ups and frustration.
Faster, more accurate quoting: Get real-time cost estimates and lead times instantly, easily create sales orders, and assign special pricing arrangements with a tailored mixed-mode manufacturing ERP—so you can respond to customers faster.
Streamlined shop floor execution: With a full suite of production and engineering management tools, the best mixed-mode ERPs ensure each job gets done on time and in budget.
6. Reduced Employee Training and Improved Experience
Bringing new employees up to speed on complex mixed-mode manufacturing processes can be time-consuming and costly—especially if your systems are disjointed or require specialized knowledge for different tasks. If each department uses different tools, interfaces and workflows, training and ongoing productivity become a never-ending headache.
With a mixed-mode manufacturing ERP, that challenge disappears. Why? Because everything works under a common user experience, making training and everyday tasks faster, easier and more efficient.
Let’s look at how a mixed-mode ERP simplifies training and user experience:
Consistent interface across all functions: Whether an employee is processing a work order, checking inventory, or scheduling production runs, the look and feel remain the same—because it’s all now in one system. This means once they learn one function, they can quickly adapt to others without starting from scratch.
Automation and guidance: With automations, pre-configured alerts, guided workflows and intuitive user interfaces, advanced manufacturing ERPs unburden your staff from arduous or confusing processes. Not only does this mean quicker onboarding for new staff, but enhanced productivity in everyday use.
AI-enhanced user guidance and help features: The best mixed-mode manufacturing ERP systems come with AI assistants providing instant, context-aware support. This makes it even easier for your employees to learn as they go—without constant reliance on IT or managers.
Why Aptean Is the Right Choice for Mixed-Mode Manufacturers
You don’t need an ERP that just “works”. You need one that works for you—built to handle the realities of mixed-mode manufacturing. We get it. The complexity is real, and the wrong software only adds to the chaos. That’s why Aptean’s mixed-mode manufacturing ERP is designed specifically for companies like yours—where flexibility, efficiency and precision are non-negotiable.
With decades creating specialized software and customers across the globe, you can rest assured Aptean has the manufacturing software solutions to solve your most complex challenges. In particular, our range of industry-specific ERPs come packed with tailored features for food and beverage, fashion and apparel, discrete and process manufacturing—so you’re not constantly fighting against a generic system that doesn’t “get” your business.
What’s more, our cloud-based software gives you the flexibility to scale without disruption. Expanding to new markets? Adding production lines? Handling a spike in custom orders? No problem. Cloud technology lets you adapt quickly, access critical data from anywhere and keep IT costs low. In other words, you can focus on making great products, not managing outdated software.
And, to propel your manufacturing business ahead of the crowd and leverage the latest technology before your competitors, you can choose our AI-powered AppCentral platform that unites your entire operation with pre-connected applications including ERP, enterprise asset management (EAM), customer relationship management (CRM) and more. With AI-enabled tech you can automate processes, empower your team and turn your data into decisions that drive success.
Finally, even the best technology is only as good as the people behind it. That’s where Aptean really stands out. Our by-your-side support isn’t just about answering questions—it’s about ensuring your success. From the initial setup to everyday optimization, our experts are with you at every step, helping you solve problems, streamline processes and uncover new opportunities.
So, what does this mean for you? Less stress. More efficiency. Better results. If your current manufacturing ERP is slowing you down, maybe it’s time to rethink what’s possible. Aptean is ready when you are.
Contact us today to learn more about our industry-specific solutions or request a demo of our mixed-mode manufacturing ERP to see how it could turn your challenges into opportunities.
Related Content
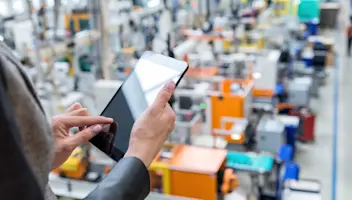

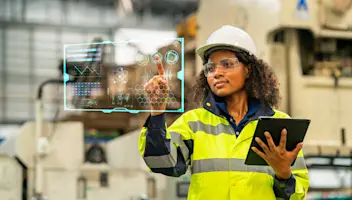
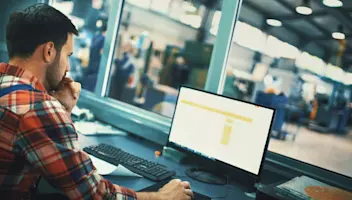
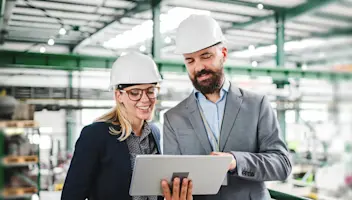
Request a callback from a manufacturing ERP expert
Discover the benefits of software designed specifically for the discrete manufacturing industry.
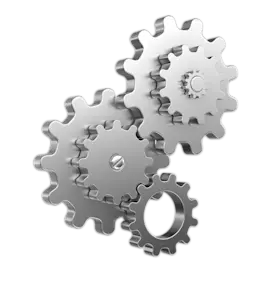