Featured in this post
Manufacturing Software Systems: The Full Scope Explained
Manufacturing Software Systems: The Full Scope Explained
Feb 5, 2024
April Matthews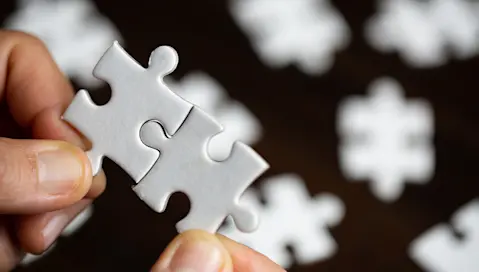
So, you’ve decided to implement manufacturing software to up your game and power your digital transformation. Now what?
There are so many different systems on the market, all promising a range of features and benefits, that planning your technology roadmap feels like a complex puzzle.
That’s why we’ve put together this list to help you fill in the blanks and solve the puzzle by exploring seven of the most common manufacturing software systems. For each one we’ll provide primary use cases, functionalities, benefits and signs your operation may need the system.
But first, let’s take a look at four foundational principles that you should apply before deciding which systems are best for your business—the edge pieces of your puzzle if you will, getting you started with a clear focus.
Start by evaluating your current tech stack—Identify any deficiencies, your current challenges and clarify your short- and long-term goals. Then you can be sure you’re only exploring technologies that can elevate your operations in line with these gaps and objectives.
Prioritize industry-specific solutions if available—Systems that are designed for your industry deliver additional benefits straight out of the box and can help you avoid costly customizations or workarounds.
Choose cloud software for a future-proof tech stack—Cloud deployment is a cornerstone of most digital transformations for obvious reasons. With it you’ll gain enhanced agility, scalability, security and flexibility.
Consider starting with one core platform—Many manufacturers choose to build their tech stack around one comprehensive enterprise resource planning (ERP) platform. So, whether you need to update your current ERP, buy your first one or replace a legacy system, it’s a good foundation to build upon.
Now we’ve got the edge pieces, let’s complete the puzzle of manufacturing software systems. Starting with that core platform—ERP.
1. Enterprise Resource Planning (ERP)
A manufacturing ERP is a comprehensive solution designed to streamline the operations of a wide variety of businesses. Like a central nervous system, this enterprise software for manufacturers seamlessly connects and coordinates many functions within your organization—from finance and sales to quality, procurement and inventory. As a result, it’s one of the most important systems your manufacturing operation will implement and should form the foundation of your digital transformation.
Primary Use Cases
Besides nearly all manufacturers, ERP software is also popular among distributors, retailers, service providers, healthcare institutions, government agencies, educational institutions, nonprofit organizations, financial institutions and even professional services providers.
Therefore, no matter which manufacturing industry you operate in, you should look for an industry-specific ERP that delivers specialized functionality tailored for your unique challenges instead of the generic features that suit the wide range of businesses listed above. After all, one-size-fits-all, doesn’t end up fitting anyone all that well. Manufacturing-specific ERP systems are available for a range of both process and discrete verticals, including food and beverage, cosmetics and apparel.
Key Functionalities
As we mentioned, ERP coordinates many different departments in your operation and in doing so, collates and standardizes their data—creating a single source of truth, with accurate and accessible information. As well as providing this fully digital and unified database that increases collaboration and reduces silos, ERP software also provides features to improve many business processes.
When comparing ERP systems key functionalities you should look for include demand forecasting, production planning, supply chain management, inventory management, bidirectional materials traceability, quality control, and reporting and analytics.
When it comes to industry-specific solutions, you’ll want to look for features that are unique to your sector, such as bills of materials (BOMs) automation for discrete manufacturers, recipe and formula management for process manufacturers, allergen management for food and beverage businesses, and vendor management for fashion and apparel brands.
Signs You Need ERP
Here are some strong indicators that implementing a manufacturing ERP system or updating your existing solution could benefit your operations:
Siloed data in disparate systems
Frequent data errors
Inefficient or manual processes
Lack of real-time insights
Poor inventory management
Excess waste or surpluses
Trouble fulfilling orders on time
Inconsistent product quality or safety concerns
Time-consuming workarounds
Top Benefits of ERP
The benefits of ERP are comprehensive, revolutionizing the way you operate and manage your resources. By automating many of your processes, ERP enables your team to focus on higher-value or strategic tasks, which is critical if you’re operating with a lean workforce or trying to combat global talent shortages.
Streamlining manufacturing processes like this enables you to increase operational efficiency, improve workforce productivity, reduce waste and better utilize all your resources—ultimately unlocking significant cost savings and boosting profitability. Plus, better document and data management, greater visibility and increased collaboration also help you ensure stricter regulatory compliance, enhance scalability and enable faster, data-driven decision making—so you’re better equipped to drive business growth.
Additionally, manufacturing ERP software enables you to manage and enhance customer relationships and improve the quality and consistency of your product, leading to greater customer satisfaction. With happier customers, streamlined operations and lower costs, ERP delivers immediate benefits to help you gain a competitive edge.
2. Enterprise Asset Management (EAM)
EAM software monitors and helps you manage labor-intensive equipment throughout its lifecycle—from planning and optimizing necessary upkeep work to keeping detailed records of maintenance history. As they are frequently discussed together, it’s important to note that EAM software offers all the capabilities of a computerized maintenance management system (CMMS) and many more.
Primary Use Cases
If machinery plays a crucial role in your manufacturing processes, then EAM can be valuable for your organization. Other businesses heavily relying on physical assets, like those in the transportation, equipment, construction and healthcare sectors, should also consider EAM.
Key Functionalities
Using EAM software, asset-intensive businesses like yours can leverage capabilities such as equipment tracking, preventive maintenance scheduling, inventory and work order management and Internet of Things (IoT) integration.
Moreover, the system provides a centralized repository for all machinery manuals, maintenance procedures and other essential documents for easy access. So, you’ve always got the information you need to keep production on track and maximize output.
Signs You Need EAM
Your organization should think about implementing an EAM system if you’re dealing with any of these challenges on a regular basis:
Frequent or extended unplanned equipment downtime
Equipment at the end-of-lifecycle
Inefficient maintenance practices
Increasing maintenance costs
Poor asset visibility
Complex asset portfolio
Inconsistent maintenance data and documentation
Decreasing customer satisfaction as a result of recurring machine failure
Top Benefits of EAM
Implementing EAM software helps you streamline maintenance processes, promote excellent equipment uptime and prolong asset life while optimizing resources and enhancing reliability.
It also enables you to implement proactive and preventive maintenance, automate repetitive tasks like ordering parts or restocking inventory and maximize asset utilization. All of this combines to boost operational efficiency and help control costs while maintaining consistent productivity thanks to reliable, well-maintained assets.
3. Overall Equipment Effectiveness (OEE)
As most manufacturers know, OEE is a key metric in production to understand, assess and enhance manufacturing performance. OEE software integrates with shop floor-level devices to help you better understand the efficiency of your assets and optimize your OEE score.
Primary Use Cases
OEE software is for manufacturers of all kinds. Whether your business focuses on personal care and cosmetic items; food and beverage products; apparel; computers; electronics; fabricated metals; electrical equipment; transportation equipment; or any other category, an OEE system can help you better utilize your manufacturing equipment.
Key Functionalities
At its core, the software captures all necessary data and then automatically calculates OEE scores, allowing you to leverage those metrics to assess the performance of equipment and processes on the shop floor. In addition, OEE provides increased visibility into real-time performance scores, robust visualizations, mobile accessibility and direct integration with machinery to give you the insights you need, when you need them.
More advanced capabilities include cost and profitability monitoring including operator functions. For example, you can use production monitoring and optimization capabilities with easy-to-use tools to help you efficiently analyze production data and implement improvements.
Signs You Need OEE
Consider implementing OEE software as part of your manufacturing software puzzle if your business is often facing any of these operational issues:
Missed production targets
Low return on investment (ROI) on raw materials
Lack of actionable insights into what prevents efficient performance
Excessive rework due to malfunctions
Poor schedule attainment
Top Benefits of OEE
An OEE system offers benefits to both your management and shop floor by providing not only a measurable goal, but ways to reach it, too—then they can celebrate whenever an improvement boosts production efficiency.
OEE also promotes shop floor accountability, consistent production volume, process efficiency, minimal idling time, reduced waste, scrap and rework—all of which helps you address the Six Big Losses, get the most out of both your personnel and machinery and maximize productivity.
4. Product Lifecycle Management (PLM)
PLM software helps you handle the data and processes involved in the full product lifecycle—from conception, design and development to production, launch, maturity and retirement. In short, it helps your business manage the new product development (NPD) process systematically, making the needed information easily accessible—with tools that help in the successful and timely completion of each step along the way.
Primary Use Cases
Any business involved in designing and manufacturing consumer goods can benefit from PLM software to help round out their manufacturing systems puzzle. Just like ERP systems, some vendors offer PLM that’s specific to your industry, delivering deeper benefits and quicker ROI—whether that’s a PLM for food and beverage companies, software for cosmetics and personal care, or an apparel PLM system.
Key Functionalities
Serving as an organization-wide, fully digital platform, PLM has all the features your entire team needs to manage your design and production data—with tools to streamline communication, marketing, packaging and compliance.
In particular, when completing your PLM software selection process look for tools for the management of recipes and formulas, bills of materials (BOM), product iterations, documents, compliance, quality and supplier relations. The best PLM systems also provide features to improve communication and collaboration such as system-wide commenting, labeling, task assignment, calendars and hand-off processes.
Signs You Need PLM
If you’re struggling to differentiate your business from competitors and broaden your market share, a tailored PLM system can help you deal with the following challenges:
Products take too long to get into the market
Lack of data visibility for everyone involved in the NPD process
Duplicate and inconsistent data entries
Regulatory compliance and recall concerns
Increasing operating and commodity costs
No efficient collaboration platform with external partners
Top Benefits of PLM
One of the biggest benefits of PLM software is the way it consolidates your product lifecycle data in a unified database that’s accessible by all departments, so you can increase efficiency across the NPD process, boost collaboration across teams, better determine revenue opportunities and analyze profit margins with pinpoint accuracy.
You can say goodbye to workflow disruptions in your product development process as PLM helps you identify and eliminate errors before they even happen. Moreover, with increased efficiency and collaboration, you’re able to better capitalize on emerging opportunities and get your product to market quicker, improving profitability and positioning your brand above your competition.
5. Transportation Management System (TMS)
TMS software is comprised of various modules and tools that optimize distribution processes—from capacity management and truck route planning to final mile customer service and driver task management. With powerful TMS software solutions you’re empowered to create customer-centric and cost-effective logistics operations.
Primary Use Cases
Transportation management systems serve businesses that distribute products, and sometimes services—from manufacturers and retailers that transport their own products to distributors and third-party logistics providers that deliver on behalf of brands. Advanced TMS software can help with even the most complicated, high-volume, multi-facility shipping operations.
Key Functionalities
The core of most TMS software lies with route optimization tools. From basic static routing to advanced continuous optimization engines there are many levels of sophistication. Most businesses should look for a system that includes advanced algorithms that consider your business variables such as customer time windows, driver and vehicle availability, product sizes and many more.
Other high priority TMS capabilities include strategic route planning, customer communication management, live management and route execution control, electronic proof of delivery, territory and workload balancing tools, and capacity management.
A TMS should also have cutting-edge analytics tools and a centralized hub for your logistics data, including key performance indicator (KPI) dashboards empowering you to monitor and control performance in real time.
Signs You Need TMS
If you’re facing any of these issues on a regular basis, it’s time to consider implementing TMS tools:
Repeated shipping delays and missed delivery times
Increasing logistics expenses
Difficulty optimizing carrier selection and load consolidation
Poor real-time shipment tracking visibility
Trouble retaining or satisfying drivers
Time-consuming or manual route planning processes dependent on employee knowledge
Inability to satisfy customer demands for timed deliveries or detailed final mile communication
Top Benefits of TMS
The best TMS software enables you to provide excellent final mile customer service to differentiate your brand while tightly controlling and reducing transportation costs. Together this helps turn your distribution operation from a cost center to a profit driver.
With advanced TMS tools you can cut planning time from hours to minutes, reduce logistics costs by up to 30%, improve driver satisfaction and retention, gain real-time visibility of your entire operation, improve your cost to serve analysis, and create a continuous improvement loop with advanced reporting and what-if scenario modeling.
Customer services benefits include the ability to offer more delivery options that you can reliably satisfy, accurate and timely final-mile communications, paper-free on-site encounters, and real-time delivery tracking.
6. Warehouse Management System (WMS)
A WMS helps your business manage warehouse inventory, staff and your supply chain in the most efficient and accurate way possible. Because a lot of complicated actions take place inside your storage facilities, you need a robust solution that allows you to efficiently oversee everything in real time.
Primary Use Cases
Other than discrete and process manufacturers businesses with complex inventories, like ecommerce retailers, distributors, apparel brands and construction material suppliers, may consider implementing WMS.
Many of these companies choose to implement a manufacturing ERP system with in-built WMS functionalities to avoid needing two overlapping systems.
Key Functionalities
From real-time inventory tracking, warehouse location control and order management to picking and packing tools, shipping integrations and reporting capabilities, the features of a good WMS are designed to streamline your warehouse processes from receiving to dispatch, even covering returns when necessary.
Many WMS systems also offer a range of integrations and compatibilities, allowing you to empower workers with scanners, mobile devices and seamless integration with other systems such as ERP and TMS software.
Signs You Need WMS
Below are the key indicators that your business could benefit from WMS functionality:
Increasing stock complexity and volume
Repeated inventory inaccuracies and errors
Lengthy order processing times
Poor visibility of finished goods and raw materials
Growing customer demands for quicker order fulfillment
Suboptimal use of warehouse space
Consistent issues with food safety or environmental regulators
Top Benefits of WMS
With WMS functionality, your business can increase visibility and control from receiving and packing to stock counts and shipping—improving operational efficiency and ensuring optimizing resources, from space to staff time.
Robust WMS software streamlines order fulfillment by optimizing picking routes and minimizing errors, ensuring a seamless end-to-end workflow. With this additional visibility and streamlined processes you’re able to improve inventory control and reduce write-offs, fines and fees.
Additionally, WMS functionality integrates real-time data analytics, offering actionable insights into inventory trends and demand fluctuations, leading to proactive and informed decision-making.
7. Business Intelligence (BI)
BI is a powerful software solution for manufacturing businesses that facilitates data-driven decision-making. With the ability to analyze data from multiple sources, including your ERP system, BI software offers intuitive tools for data visualization and analysis that help you make the best strategic decisions for improvement.
Primary Use Cases
You can gain value from BI software no matter the industry you operate in or the size of your company. Your business executives, managers, analysts, marketing, sales, accounting and IT staff members can all use the analytics platform to transform data into actionable insights.
Key Functionalities
BI has tools to extract data from many sources, from spreadsheets to more sophisticated databases and other manufacturing software systems. It then collates all this data and transforms it into interactive dashboards, charts and reports. Good BI systems also offer the ability to manipulate data and customize reports on a user level so that each of your departments can focus on the insights they need.
The best BI systems will provide KPIs, metrics and visualizations tailored to your industry as standard and allow you to create your own reports for business-specific requirements. Ensuring all the data you need is available exactly when you need it without complicated processes.
Signs You Need BI
You should consider implementing business intelligence software in your business if you’re experiencing any of the following:
Data overload
Inaccurate reporting
Slow or “blind” decision-making
Lack of data integration
Unreliable forecasting
No customer insights
Poor performance monitoring
Discrepancies in data between departments
Top Benefits of BI
Thanks to the variety of systems we’ve covered in this blog, most manufacturing operations today have no shortage of data. What they lack is the ability to distil all that information into actionable insights. The biggest benefit of BI software then is to maximize the value of all that data swimming around your business—creating a single source of truth, helping you identify trends, spot areas for improvement and ultimately, make more informed decisions.
With faster, data-driven decisions, you can improve efficiency, reduce costs, enhance workflows and more, boosting performance across a variety of departments and processes.
BI can also help you react quickly to and understand customer behavior, empowering you to identify patterns and fix issues based on detailed reports and actionable insights—helping you improve service and boost profitability.
Complementary Manufacturing Software Systems To Complete Your Digital Ecosystem
That covers the seven biggest solution pieces to consider when completing your manufacturing software puzzle and planning your digital transformation journey. But there are a few other honorable-mention puzzle pieces—the ones that sometimes get lost in the sofa cushions but are necessary to complete the picture, so to speak. You’ll want to evaluate these depending on your existing tech stack and business requirements, but most manufacturing companies can benefit in some way from the below.
Customer relationship management (CRM) - Gives you a complete view of all customer data and streamlines interactions to save you time and improve customer service. As well as standalone advantages there are many benefits of CRM and ERP integration for your manufacturing business.
Electronic data interchange (EDI) tools - Streamlines the exchange of documents between you and your business partners or suppliers to speed up communications and eliminate fines or chargebacks. Look for EDI systems that are either built-in or fully integrated with your ERP to gain the most value.
Payment processing software – Digitizes payment processing and automates reconciliation to ensure you get paid faster, streamline processes and improve financial reporting.
Shop floor control (SFC) - Helps you master shop floor execution with tools to enhance processes, increase visibility and boost productivity. Again, best utilized in conjunction with a powerful ERP for the best results.
No matter what solutions you end up deploying as part of your digital transformation strategy, focusing on those foundational concepts we laid out at the start of this blog—in particular choosing industry-specific, cloud software—will ensure you only select systems that can truly elevate your business and bring measurable benefits.
Adding the Final Piece of the Puzzle: A Proven Vendor To Elevate Your Manufacturing Business
Now, you’ve got most of your manufacturing software puzzle laid out and the picture is finally becoming clear, it’s time to slot in that last piece. The one that takes it from “almost there” to "all buttoned up”—that’s a vendor you can rely on.
When tackling as complex an organizational shift as digital transformation, you’ll need a trusted partner that’s in your corner and can offer advanced solutions, proven expertise and comprehensive support. Enter Aptean.
Our suite of industry-specific software offers specialized functionality to help solve the unique challenges of your sector straight out of the box—something that generic solutions with time-consuming workarounds and costly customizations just cannot offer. Plus, the deep industry expertise, best-practice knowledge and by-your-side support of our in-house teams ensures straightforward implementations, deeper realization of benefits and quicker ROI.
What’s more, we offer flexible cloud software solutions to future-proof your tech stack. With cloud implementations on a Software as a Service (SaaS) model, you can avoid hardware costs, improve accessibility, enhance security and unlock greater scalability. So, you have the agility and reliability you need to grow your business.
Finally, selecting one vendor for all your manufacturing software systems offers many benefits, helping to ensure all your puzzle pieces fit snugly together. By choosing us as your complete manufacturing digital transformation partner you can achieve smoother integrations, receive dedicated support, avoid the complexity of communicating with multiple vendors and easily add new systems or functionality when you need to. So, you’ll always be Ready for What’s Next, Now®.
Ready to start your digital transformation? Get in touch with one of our solutions experts today or explore our range of manufacturing software systems.
Ready to future-proof your business with cloud software?
We’ve got the industry-leading software and experts to help your business thrive.
