Building a Maintenance Program for the Future
Building a Maintenance Program for the Future
Building a Maintenance Program for the Future
Dic 12, 2018
Kay Jenkins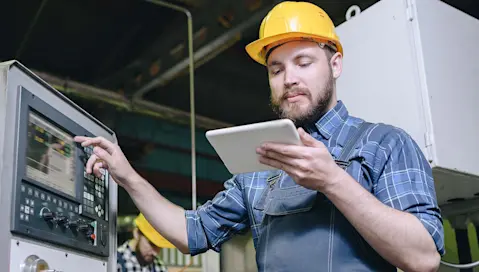
It’s easy to get overwhelmed by the daunting prospect of developing an advanced maintenance strategy, especially if you’re a small- or medium-sized manufacturer.
But relying solely on preventive maintenance, which does little against random breakdowns that cause the majority of asset failures and is often conducted too often, can be costly.
Getting to where you can predict breakdowns before they happen doesn’t need to happen overnight. It’s a steady progression of collecting the data right in front of you and studying it over time for insights you can use to make smart decisions.
Here are three key steps that will help you head towards a proactive maintenance approach.
Collecting the Data
Condition-based maintenance, where asset conditions can trigger maintenance activity, are a good way to combat the random failures that make up nearly 90 percent of all asset failures, according to IBM. Such an approach requires data, either directly from sensors or input by operators into an enterprise asset management (EAM) system. Wireless sensors, which prevent disruption to operations, can record production counts, rejects, temperatures, humidity, and pressures.
Taking a Closer Look
It’s not just enough to compile data. Now you need to figure out what to do with it. A reliability engineer can scour it for trends and patterns, identify when those random breakdowns occur, and dig beneath the surface to discover root causes. That kind of analysis can be a powerful tool, helping you spot the signs of an impending failure. With those warning signs in hand, you can take action to prevent a failure ahead of time.
Moving to the Next Level
Creating the smart factory of tomorrow is more than just having a human react to data coming in. You want to empower your connected systems to spot those signs and symptoms and correct problems. In this model, data flows from connected assets and your system reacts in real time, generating tickets, ordering parts, and shifting production schedules as needed, automatically.
Learn more about how to move toward the advanced data-driven maintenance program of the future from Kay Jenkins in Manufacturing Business Technology.
Related Content
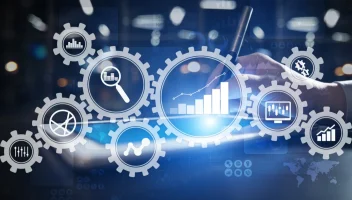
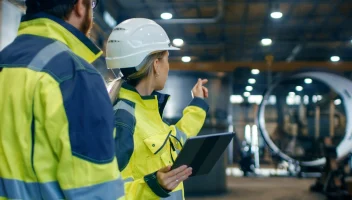
¿Todo listo para transformar tu negocio?
Tenemos las soluciones EAM especializadas que necesitas para superar los desafíos de tu sector.
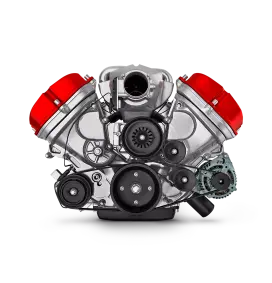