Monogram Foods Harnesses the Power of Aptean Process Manufacturing OEE for Greater Accuracy, Visibility and Efficiency
Monogram Foods Harnesses the Power of Aptean Process Manufacturing OEE for Greater Accuracy, Visibility and Efficiency
Monogram Foods Harnesses the Power of Aptean Process Manufacturing OEE for Greater Accuracy, Visibility and Efficiency
12 Jan 2022
John McCurdy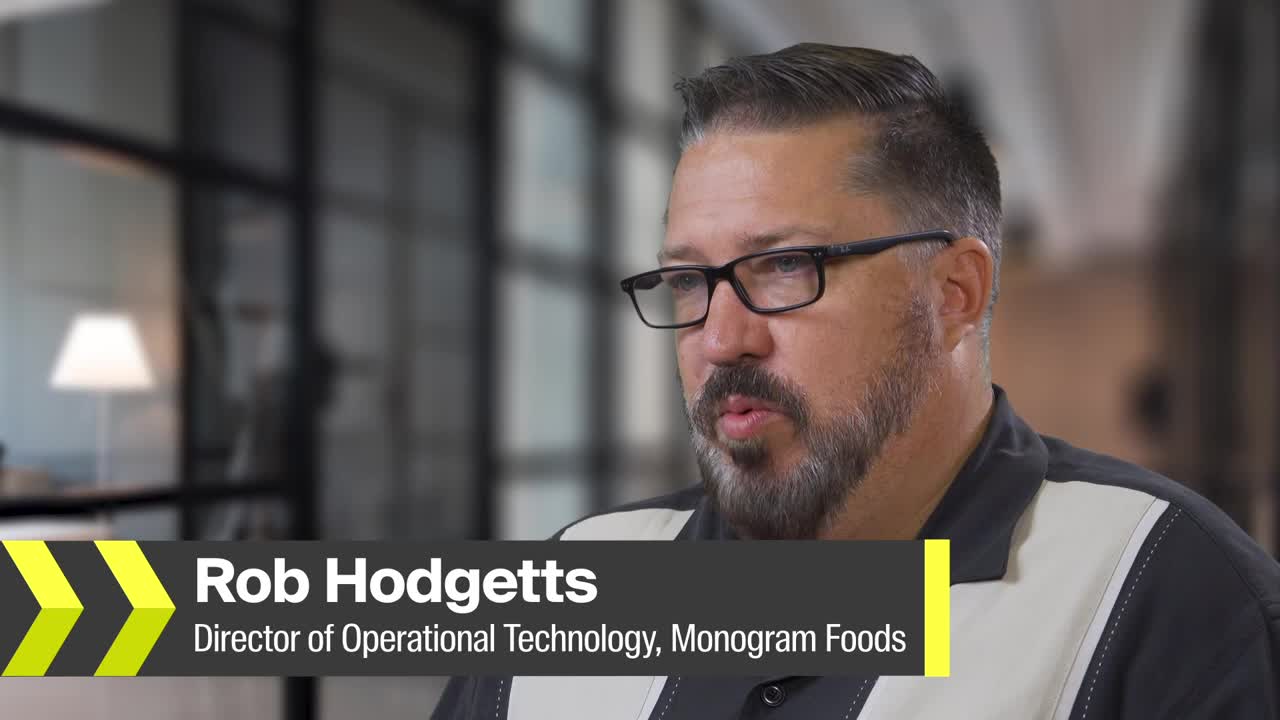
Monogram Foods, a U.S. food manufacturer founded in 2004, has seen considerable growth since its inception. Today, it has more than 3,000 employees across 10 facilities in six states.
As the business expanded, though, its paper record-keeping methods started to become a liability, resulting in data inaccuracies, delays in reporting and a lack of insight for smarter decision-making. This, in turn, was making it more difficult for the company to prepare for audits.
“Our inspector would have access to all of our paperwork off the line. Sometimes they’d get a big thick stack of paperwork, when really the USDA only needs to see a few of those,” said Rob Hodgetts, director of operational technology at Monogram.
These difficulties prompted the organization’s leaders to seek a solution that would help them convert to a full digital interface. They found Aptean Process Manufacturing OEE, with its real-time performance management, paperless compliance and robust analytic capabilities, to be the perfect fit.
“Now, the inspector can go into the system, see it in real time and see that we are in control of our CCPs,” said Hodgetts. “And then if they’ve got a question on our history, they can go back in the system and pull the data out themselves, which frees up our quality folks.”
This has greatly simplified the matters of passing audits, giving Monogram’s staff the peace of mind to focus on what they do best—make the best food they can, with the greatest efficiency possible.
“We’re always going to be engaged with the USDA, but as far as spoon-feeding them the data, we don’t have to do that anymore,” Hodgetts said. “The inspector has it at their fingertips and can ask questions as needed.”
Converting to a fully digital database and interface has had other positive results. One is greater accuracy by eliminating the chance of manual errors in logging figures and readings.
“The way that we built it in Aptean Process Manufacturing OEE, it prevents ‘fat-fingering,’” said Hodgetts. “A lot of times, as we all know, there’s human error when using a pen or pencil to fill out our quality checks. Now, our paperless system confirms that the data is correct.”
Better access to and visibility of key metrics has also been of huge benefit at Monogram. All team members are better informed on how operations are running and the results they’re achieving.
“Before we had Aptean Process Manufacturing OEE, we’d have to take some folks, lock them in a room with a big thick stack of papers, and then they would have to manually take that data—which may or may not be right—and type it into an Excel spreadsheet,” Hodgetts said. “Considering the amount of data can be overwhelming, we found we weren’t getting the data into any kind of system that allowed us to do an analysis.
“Now we can do real-time analysis and pull 90 days’ worth of data on a specific product. That helps us make smarter business decisions, because the data is reliable,” Hodgetts concluded.
Monogram Foods is beyond pleased with the improvements they’ve already seen as a result of implementing Aptean’s OEE solution for food and beverage. The system has facilitated better performance in a number of areas, including transparency and productivity.
“Aptean Process Manufacturing OEE has exceeded our expectations in that the visibility in the system is fantastic,” said Hodgetts. “Our team members are very attuned to what’s happening on the line, including downtime, slow runs and quality control. This system has provided a great return on investment through improved material variances and improved uptime.”
Efficiency is also up at Monogram. Considering their large daily outputs across a wide range of meat snacks, appetizers, sandwiches and baked goods, they highly value the ability to get more out of their equipment and materials.
“All in all, we’ve had a significant uptick in overall equipment effectiveness at all of the plants where we’ve installed it,” Hodgetts said. “We’ve seen a rise of 10 points in OEE, and those in the food industry running high-volume lines will recognize that’s a big number.”
Hodgetts attributes much of their success with the new platform to the factory floor staff. They’ve embraced their new methods and responsibilities and taken ownership over the system.
“A lot of this is based on buy-in from the folks on the floor,” said Hodgetts. “We all know the data’s credible, we can all take action based on the data in real time, and that drives our utilization, our yield and our overall equipment effectiveness to improve on a regular basis.”
Ask him what he thinks of Aptean’s solution, and Hodgetts’ opinion is clear.
“Would I recommend Aptean Process Manufacturing OEE to others who are looking to go paperless and gain better control over their processes? Absolutely,” he said. “It’s caused a change in culture. Certainly the bells and whistles are nice, but it’s really exciting when you see folks engage with the technology.”
If you want to know more about how Aptean Process Manufacturing OEE can drive better outcomes at your food and beverage business, contact us today.
Related Content


Klaar om uw bedrijf naar een hoger niveau te tillen?
We hebben gespecialiseerde OEE-oplossingen waarmee u elke uitdaging in uw branche aankunt.
