Uitgelicht in deze blog
Drie belangrijke factoren die jouw OEE score beïnvloeden
Drie belangrijke factoren die jouw OEE score beïnvloeden
15 Jan 2020
Aptean Staff Writer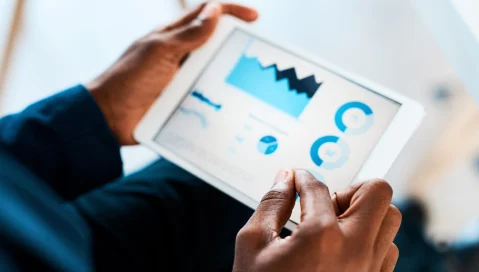
Overall equipment effectiveness (OEE) is een vaste standaard die wordt gebruikt bij het meten van de productieproductiviteit. In eenvoudige bewoordingen is OEE een term die wordt gebruikt om te evalueren hoe efficiënt een fabriek wordt gebruikt. We kunnen stellen dat OEE wordt gebruikt in de productie om productiemanagers of exploitanten van fabrieken te helpen bij het bepalen van problemen in hun activiteiten, het identificeren van het percentage dat de productietijd heeft beïnvloed, het bieden van een oplossing en een standaardmeter voor het volgen van de voortgang. Het is vanzelfsprekend dat continue verbetering de belangrijkste doelstelling van OEE is.
Hoe wordt OEE gemeten?
Uit de bovenstaande definitie van OEE, kunnen we terecht en eenvoudig opmarken dat het een krachtige meting is. Dit om de eenvoudige reden dat OEE zinvolle gegevens in één enkel nummer kan bieden. OEE gebruikt meer dan één aspect om de productieproductiviteit te meten, namelijk door beschikbaarheid, prestaties en kwaliteit et is aan de productiemanager om deze correct te interpreteren en de informatie te gebruiken om de productie aanzienlijk te maximaliseren. OEE wordt vaker wel dan niet gebruikt als een benchmark om een aantal dingen te vergelijken, zoals bijvoorbeeld de efficiëntie van de eigen apparatuur.
Een aantal OEE standaard benchmarks omvatten het volgende;
100% OEE. Deze score wordt beschouwd als de perfecte productie. Dit is wanneer een productiebedrijf zo snel mogelijk alleen kwaliteitsonderdelen produceert zonder downtime.
85% OEE. Deze score vertegenwoordigt een score van wereldklasse voor fabrikanten in de discrete productie en veel fabrikanten streven ernaar om deze score als hun langetermijndoel te bereiken.
60% OEE. Dit is een normale score voor de meeste fabrikanten en geeft aan dat er ruimte is voor verbetering.
40% OEE. Er wordt gedacht dat dit voor de meeste fabrikanten een lage score is, maar dit is een normale score wanneer ze starten met het volgen en verbeteren van hun prestaties. Deze score kan eenvoudig worden verhoogddoor het toepassen van maatregelen, zoals het implementeren van OEE of het gebruik van een Manufacturing Execution System (MES).
Hoewel deze absolute cijfers zinvol kunnen zijn, is het belangrijkste dat er een positieve evolutie en trend te zien is waarbij er een verbetering is in de cijfers vanwege de genomen acties.
Overall Equipment Effectivenes is misschien wel het beste hulpmiddel voor productiemanagers en werknemers die op de fabrieksvloer werken om prestaties te verbeteren. Enkele van de termen die worden gebruikt in de statistieken op de fabrieksvloer zijn:
Target. Een term die wordt gebruikt om het realtime productiedoel ann te geven.
Actual. Dit wordt gebruikt om de werkelijke productietelling weer te geven.
Efficiency. Het werkelijke percentage (%) van hoe ver vooruit of achter de productie ligt.
Downtime. Deze term wordt gebruikt om de tijd weer te geven dat de apparatuur niet wordt gebruikt. Dit nummer wordt in realtime bijgewerkt en bevat alle niet-geplande stoptijd voor elke dienst.
Veelgebruikte termen in OEE
Voordat we overall equipment effectiveness in meer details bespreken, kijken we eerst naar enkele veelvoorkomende termen;
Fully Productive Time. Dit betekent simpelweg de productietijd nadat alle verliezen in rekening zijn genomen.
Planned Production Time. Dit vertegenwoordigt de totale tijd die een apparaat of systeem naar verwachting zal produceren.
Ideal Cycle Time. Dit geeft de tijd aan die een apparaat nodig heeft om één onderdeel te produceren.
Run Time. Dit is de tijd dat het systeem actief is en waarop de productie gepland is.
Total count. Dit betekent het totaal van alle geproduceerde onderdelen, inclusief die met defecten.
Good count. Dit vertegenwoordigt de geproduceerde onderdelen die voldoen aan de normen voor kwaliteitscontrole.
Good parts. Dit vertegenwoordigt de onderdelen die zijn geproduceerd en voldoen aan de gestelde normen en hoeven daarom niet opnieuw te worden uitgevoerd.
Quality. Deze term wordt gebruikt om de geproduceerde onderdelen te beschrijven die voldoen aan de normen voor de kwaliteitscontrole.
Performance. Deze term staat voor het totale aantal keren dat er vertragingen of korte stops zijn in de productie. Zoals eerder aangegeven, betekent een perfecte prestatie (100% score) dat de bewerking zo snel mogelijk wordt uitgevoerd. De formule voor het berekenen van de Performanceis (Ideal Cycle Time * Total Count) / Run Time.
Availability. Dit is de term die wordt gebruikt om de geplande en niet-geplande downtime te beschrijven. Een perfecte score voor beschikbaarheid beschrijft een operatie die constant draait tijdens de geplande productietijd. Dit wordt berekend door: Run Time /Planned Production Time.
Dus, hoe bereken je OEE?
Het eerste wat we moeten doen voordat we de overall equimpent effectiveness kunnen berekenen, is een onderscheid maken tussen de termen effectiviteit en efficiëntie.
In grote lijnen is effectiviteit de relatie tussen wat technisch mogelijk is om te produceren en het werkelijke product dat aan het einde van een productieperiode wordt geproduceerd. Als je bijvoorbeeld apparatuur hebt die technisch 100 producten per uur kan produceren en er slechts 80 worden geproduceerd, kunnen we zeggen dat de apparatuur voor 80% effectief is. Simpel toch?
Deze berekening houdt echter geen rekening met veel dingen die in een productiecyclus zitten, waaronder het aantal operators, stroom en de materialen die nodig zijn om de machine voor 80% effectief te maken. Daarom vertelt de bovenstaande berekening niet hoe efficiënt de machine is. Laten we zeggen dat een machine voor 60% effectief werkt wanneer deze door één werknemer wordt bediend, maar dezelfde machine werkt voor 75% wanneer deze door 2 werknemers wordt bediend. Dan kunnen we nu zeggen dat de machine met een efficiëntie van 75% draait, maar de efficiëntie met 50% is afgenomen vanwege arbeid.
Er zijn een aantal manieren om OEE te berekenen. We zullen in dit artikel de twee voornaamste manieren bekijken:
Simple Calculation. Dit is misschien wel de eenvoudigste manier om OEE te berekenen en wordt bepaald door de verhouding tussen volledig productieve tijd en geplande productietijd. OEE = (Good count x Ideal Cycle Time) / Planned Production Time.
Preferred Calculation. Dit is een veelgebruikte formule en is tot stand gekomen door rekening te houden met drie OEE-factoren (beschikbaarheid, prestaties en kwaliteit). OEE = Beschikbaarheid x Prestaties x Kwaliteit. De term is bedacht vanwege het allesomvattende karakter bij de berekening van OEE. Dit betekent simpelweg dat je niet alleen een nauwkeurige OEE-score krijgt over hoe goed je het doet, maar ook dat je specifieke scores krijgt voor de drie factoren, waardoor je de specifieke oorzaken van je verliezen kent.
Beschikbaarheid
Laten we eens kijken naar de gewenste berekening aan de hand van een voorbeeld. In een bepaalde fabriek duurt een normale dienst 480 minuten. De operators nemen tijdens hun dienst pauzes die in totaal 60 minuten duren. Ze doen ook 2 omschakelingen tijdens de dienst met in totaal 60 minuten stilstand van de machine. Dit resulteert in een totaal van 180 minuten verloren tijd. Daarom kunnen we de beschikbaarheid berekenen door 180 minuten af te trekken van de totale 480 minuten, wat neerkomt op 300 minuten of 62,5% beschikbaarheid.
Prestaties
Laten we nu kijken naar het prestatiegedeelte van diezelfde fabriek waar 60 producten per minuut worden geproduceerd. Van de beschikbare minuten 300 minuten zoals hierboven beschreven, kan de fabriek 18.000 producten produceren. Laten we aannemen dat de machines niet met een capaciteit van 100% werken, maar in plaats daarvan langzamer werken, met een cyclustijd van 1,5 seconde. Hierdoor wordt de maximale snelheid met 2/3 vertraagd en daardoor worden de werkelijke prestaties aanzienlijk verlaagd tot 12.000 producten of 66,7% prestaties.
Kwaliteit
Laten we tot slot kijken hoe we het kwaliteitsgedeelte van deze fabriek kunnen berekenen. Stel dat van de 12.000 geproduceerde eenheden er 3.000 niet voldoen aan de kwaliteitsnormen, waardoor de kwaliteit van de geproduceerde eenheden 75% is, d.w.z. (12.000 – 3.000 defecten) / 12.000 * 100 = 75% kwaliteit.
Uit de bovenstaande gegevens kunnen we nu de OEE berekenen door de metrics van Beschikbaarheid x Prestaties x Kwaliteit = OEE te vermenigvuldigen. OEE = 62,5% * 66,7% * 75% = 31,25%. Dit betekent dat de fabriek 28.800 eenheden kan produceren, maar er slechts 9.000 produceert.
Dit zijn de verliezen die samenhangen met OEE
Zoals eerder aangegeven is het doel van het gebruik van OEE het elimineren of verminderen van de meest voorkomende oorzaken van machinegerelateerd productiviteitsverlies. Ze staan bekend als de zes grote verliezen. Deze verliezen zijn echter onderverdeeld in drie hoofd-OEE-categorieën; beschikbaarheid, prestaties en kwaliteit.
1. Verliezen die gepaard gaan met beschikbaarheid
Verliezen als gevolg van uitval van apparatuur. Dit zijn verliezen als gevolg van apparatuur die niet werkt wanneer deze gepland is voor productie, waardoor er ongeplande downtijd wordt veroorzaakt. Enkele veel voorkomende voorbeelden van apparatuurstoringen zijn; machinestoring, problemen met gereedschap en niet-geplande onderhoudsstops.
Verliezen als gevolg van instellingen en aanpassingen. Dit zijn verliezen als gevolg van productiestilstand veroorzaakt door omschakelingen, machine- en gereedschapsaanpassingen, gepland onderhoud, inspecties en instellingen.
2. Verliezen die gepaard gaan met prestaties
Verliezen veroorzaakt door inactiviteit en kleine stops. Meestal aangeduid als kleine stops, omdat het voorkomt wanneer een machine voor een korte periode stopt. Inactiviteit en kleine stops worden ervaren als gevolg van storingen, belemmeringen voor de doorstroming, verkeerde instellingen of reiniging. Zoals je ziet, zijn dit kleine problemen die normaal gezien worden opgelost door de operator.
Verliezen door verminderde snelheid. Dit zijn verliezen die optreden wanneer een machine niet op de hoogste snelheid draait, normaal aangeduid als Ideal Cycle Time (de snelst mogelijke tijd). Verminderde snelheid wordt soms ook langzame cyclus genoemd. Enkele veel voorkomende oorzaken van verminderde snelheid zijn; slechte omgevingsomstandigheden, versleten of slecht onderhouden apparatuur en slechte smeermethoden van machines.
3. Verliezen die gepaard gaan met kwaliteit
Procesdefecten. Dit zijn verliezen als gevolg van de productie van een defect onderdeel dat tijdens een stabiele productie is geproduceerd. Dit kunnen afgedankte onderdelen zijn en onderdelen die opnieuw moeten worden bewerkt. Procesdefecten zijn het gevolg van onjuiste machine-instellingen, operator- of apparatuurfouten.
Verminderde opbrengst. Ze zijn min of meer hetzelfde als procesdefecten. Het enige verschil is dat ze worden geproduceerd vanaf het opstarten tot stabiele productie is bereikt. Ze omvatten ook afgedankte onderdelen en onderdelen die opnieuw moeten worden bewerkt. Net als procesdefecten ontstaan verminderde opbrengsten als gevolg van omschakelingen, onjuiste instellingen en opwarmen van machines.
Voordelen van OEE om de productie te verbeteren
Het implementeren van OEE kan het verschil betekenen tussen een fantastische fabriek en een goede fabriek. Het is het beste hulpmiddel voor productiemanagers die hun productiedoelen willen bereiken. Hier zijn enkele voordelen die je krijgt als je OEE implementeert.
Return on Investment (ROI) voor apparatuur. We weten allemaal dat bedrijven veel geld uitgeven aan de aanschaf van machines. Dus waarom maximaliseren ze niet het rendement van deze investering? Een eenvoudige manier om dat te doen, is door een OEE-strategie te gebruiken waarmee je gemakkelijk 15% meer eenheden kunt produceren met dezelfde apparatuur in dezelfde hoeveelheid tijd.
Concurrentiepositie versterken. Het is altijd de bedoeling van fabrikanten om verliezen tijdens de productie te verminderen en zo een sterke concurrentiepositie te bereiken. Door OEE te implementeren, kun je realtime gegevens over knelpunten of productiezwaktes verkrijgen, zodat je onmiddellijk actie kan ondernemen.
Lagere machinekosten. Een van de grote voordelen van het gebruik van OEE is de mogelijkheid om nauwkeurig de prestaties van uw apparatuur te meten, zodat je weet of deze efficiënt werkt. Een ander groot voordeel van het gebruik van OEE zijn de waarschuwingen die het je geeft bij mogelijke machinestoringen en reparaties. Hiermee kan je het probleem oplossen voordat het uit de hand loopt, waardoor onderhoudskosten en uitvaltijd worden verminderd.
Maximaliseer de productiviteit van je personeel. OEE biedt cruciale informatie over de redenen waarom je downtime van de operator ervaart, geeft je productiviteitsgegevens en wijst op lange omschakelingen of insteltijden. Je kan deze informatie gebruiken om middelen op de juiste manier toe te wijzen, te bepalen waar overcapaciteit optreedt en om te helpen beslissen of je nieuwe medewerkers nodig hebt.
Eenvoudig prestaties visualiseren. In essentie draait het bij OEE om zichtbaarheid. Het gaat erom het productieproces van begin tot einde te visualiseren, zodat je productieproblemen kan visualiseren in plaats van te vertrouwen op je gevoel. Door dit te doen, kan je eenvoudig zien wat werkt en waar verbetering nodig is.
Hoe OEE wordt beheerd door MES
Technisch gezien heeft een MES als belangrijkste doel om de machines en werkstations op de fabrieksvloer te verbinden en te bewaken. Het doel van MES is in wezen het verbeteren van de productie-efficiëntie en het verzekeren van de effectieve uitvoering van productie-activiteiten.
Er kan worden gesteld dat MES een van de fundamenten is van een geïntegreerde, gekoppelde Manufacturing Operations Management (MOM)-omgeving. Eenvoudig gezegd kan een MES worden gezien als een geautomatiseerd controlesysteem dat is ontworpen om alle work-in-process (WIP) activiteiten op de fabrieksvloer te beheren en te controleren.
Aptean MES en WMS Objective Edition
Aptean is de leider op het gebied van geïntegreerde software en services voor MES en Warehouse Management System (WMS) voor de optimalisatie van productie- en logistieke activiteiten. Onze softwareoplossing dient als de beheer- en operatorinterface tussen geavanceerde ERP-systemen en een breed scala aan productiemachines. Deze gate-to-gate-oplossing helpt onze klanten om hun doel te bereiken, namelijk het beheersen van productie en systeemtransparantie, het verbeteren van operationele efficiëntie, het realiseren van waardevolle gegevens en het vergroten van de winstgevendheid van bedrijven.
Aptean MES Objective Edition is een geïntegreerde oplossing met één platform dat MES en WMS combineert om complexe processen en logistiek voor discrete productie op te lossen.
Dynamische prestaties die aanzienlijke ROI genereren – meer OEE, minder verloren voorraad, minder logistieke bewegingen, voorraadtelling en meer.
Lost problemen met ‘Track and Trace’ kwaliteitsbeheer op. Helpt bij het naleven van wettelijke vereisten en het wegnemen van auditproblemen.
Eenvoudig te integreren met ERP-systemen en PLC / SCADA / IIOT-machines.
Eén gestandaardiseerde configuratie voor multi-site operatie en 24/7 systeemondersteuning.
Warehouse Management: Gate-to-gate goederenstroomverwerking en traceerbaarheid
Verkrijg volledig inzicht in de afhandeling en tracking van alle materiaalbewegingen in uw fabriek vanaf de ontvangst van de leverancier tot verzending richting de klant. De oplossing biedt gedetailleerde traceerbaarheid van materiaal en voorraadinspecties, inclusief partij- en serienummerniveau. Dit platform biedt realtime integratie tussen productie en logistiek.
De Production Logistics Engine biedt just-in-time en just-in-sequence levering van componenten aan de productielijn d.m.v. controleren voorraad, voorraad vrijgeven, picktaken groeperen entaken richting de groep controleren. Voer logistiek met toegevoegde waarde uit, zoals kitting en herverpakking, als extra service voor de eindklant.
De System Direct Logistic Task Tool toont het optimale gebruik van mensen en transportmiddelen.
Task Interleaving and Storage Management zorgt voor optimale taakverplaatsing en opslagprocessen, waaronder bulkvoorraad, palletvoorraad, mobiele rekken, verzamelplaatsen, hoogbouwmagazijn/-stellingen en Automatisch Geleide Voertuigen (AGV’s).
Productiebeheer: Verwerking en productie optimaliseren
Bereik optimale productieniveaus uit je machine- en personeelscapaciteit met deze geïntegreerde oplossing. Het systeem definieert hoe je jouw producten kan produceren met behulp van versiegestuurde stuklijsten en stuklijstspecificaties. Het zorgt voor gedetailleerde planning en vrijgave van productieorders op de werkvloer. Je kan dus eenvoudig de productieplanning aanpassen vanuit een tijdlijnweergave en alle gerelateerde bewerkingen worden automatisch geoptimaliseerd. De gebruiksvriendelijke productieweergave voor de operator geeft hem/haar controle over starten en stoppen en de mogelijkheid om ordergerelateerde registraties te voltooien. Het systeem zorgt er tevens voor dat alle labels en afdrukken correct en gemakkelijk te beheren zijn (bijv. houdbaarheidsdatums).
Registreer- automatisch of handmatig:
Personeels- en machine-uren.
Productieoutputgegevens en bepaal KPI’s voor opbrengst, First Time Right (FTR), schroot en reparatie.
Alarmen en onderbrekingen inclusief niet-ordergerelateerde indirecte operatoruren (bijv. vergadertijd).
Productregistratie.
Materiaal beheer: traceerbaarheid van materiaal tot voorraadstatus en partij- / serieregistratie
Ontvang gedetailleerde registratie van verbruikte bulk- of palletgebaseerde componenten en uitvoer in realtime. De oplossing maakt volledige traceerbaarheid van materiaal mogelijk door inline registratie van het lot en / of serienummer voor Lot Genealogy-rapporten en volledige productpaspoorten. Bekijk de realtime voorraadstatus en beschikbaarheid direct op de productielijn.
Kwaliteitsmanagement: Productiekwaliteit traceren met SPC
Beheer en definieer kwaliteitscontroles, invoer en metingen die handmatig of automatisch moeten worden uitgevoerd gedurende het gehele productieorderproces. Definieer gedetailleerde operatorinstructies om papierloos werken op het werkstation van de operator mogelijk te maken. Voeg vervolgens documenten en standaard werkprocedures toe aan een productieorder. De oplossing maakt een volledig geautomatiseerde instelling van machineparameters en lijnprinters mogelijk. Gebruik de dubbele afmeldoptie om de release te beperken tot validatie door twee gebruikers.
Samenvatting: De impact OEE op uw resultaten
OEE is in het recente verleden gebruikt om een indruk te geven van hoe goed een productieproces het doet. Hoewel dat een van de belangrijkste doelstellingen is, zal de echte waarde van het implementeren van OEE alleen worden gezien wanneer de gegevens worden gebruikt om te verbeteren, want wat gemeten wordt, wordt ook daadwerkelijk gedaan. OEE-verbetering is een van de continue verbetermaatregelen die van invloed zijn op het bedrijfsresultaat. De waarde van OEE is snel zichtbaar in minder stilstand van de machine, betere kwaliteit en meer geleverde producten, wat gelijk staat aan meer winstgevendheid.
Dus waarom zou je niet overwegen wat Aptean MES/WMS Objective Edition kan doen om je vandaag te helpen jouw OEE-efficiëntie te verbeteren? Neem contact met ons op of plan een gepersonaliseerde demo.
Gerelateerde inhoud
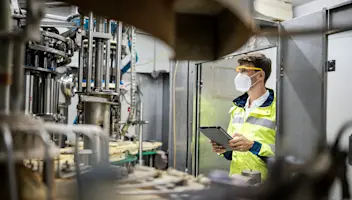
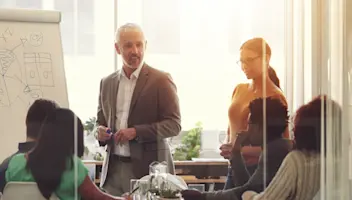
Klaar om uw bedrijf naar een hoger niveau te tillen?
We hebben de gespecialiseerde software om uw organisatie verder te helpen.
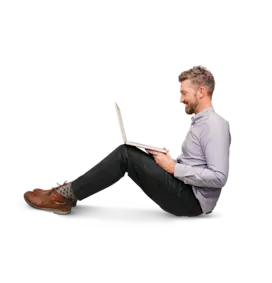