Break Free From Spreadsheets and Accelerate Growth With a Manufacturing ERP System
Break Free From Spreadsheets and Accelerate Growth With a Manufacturing ERP System
Break Free From Spreadsheets and Accelerate Growth With a Manufacturing ERP System
21 Nov 2023
Aptean Staff Writer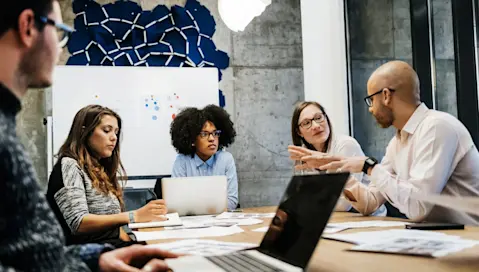
Over the years, spreadsheets have long been a trusted tool of many manufacturing businesses like yours for managing critical processes. In fact, recent statistics revealed 67.4% of supply chain managers use them regularly.
However, as demand for products and services increases, businesses frequently realize the limitations and challenges of relying on this approach. As your organization evolves, the weaknesses of workbooks and spreadsheets become increasingly apparent in managing your complex data.
From information inconsistencies to version control nightmares, cumbersome worksheets could deter smooth operations and impact your finances. An enterprise resource planning (ERP) system can level-up your game by transforming your day-to-day operations and improving overall efficiency to power your digital transformation journey.
In this blog, we’ll explore the issues caused by reliance on spreadsheets and workbooks in the manufacturing industry and discover how shifting to an ERP system tailored for your industry can help reshape the landscape of your operations.
Relying on Spreadsheets Can Stunt Growth
Whether you’re a discrete or process manufacturer, depending entirely on spreadsheets can lead to significant usability challenges. When you manually enter and manipulate data, it's easy to introduce human error. These seemingly small mistakes can quickly snowball into inventory issues, botched orders and financial discrepancies.
Accuracy is key in your industry; precision and efficiency are non-negotiable for businesses like yours and spreadsheet slip-ups can't be ignored. Speed matters, but when relying on inefficient spreadsheets to make critical decisions, your operations slow down to avoid mistakes.
Additionally, the use of spreadsheets often leads to departmental silos, with team members from various departments working on their separate spreadsheets—making access to reliable data painstakingly time-consuming when performing analysis.
Beyond that, there’s a critical business goal that spreadsheets don’t support—scalability. As your manufacturing operations expand, using this manual method will cease to be effective or even feasible in managing complex production schedules, accounting records and extensive inventories.
Navigating the Shift: From Spreadsheets to ERP
So, if you want to ditch the spreadsheets, what’s next? If you’re ready to kickstart your digital transformation journey by implementing a tailored ERP for manufacturers, you need to consider some essentials as ERP selection criteria.
Ideally, you need to conduct due diligence including in-depth research, and discuss the following with the other leaders at your company to help you achieve a seamless transition from spreadsheets to ERP:
Budget: Careful planning of finances is vital to help your leadership team understand the long-term benefits of implementing a manufacturing ERP, including other factors like probable savings, increased productivity and other potential return on investment (ROI).
Vendor: You should consider partnering with a software vendor that offers industry-specific solutions tailored to your sector’s unique challenges and requirements. Typically, a vendor with decades of extensive experience in your line of business has a team of experts who can also provide insights on how to streamline your operations further. Also, discuss with your vendor whether you want an on-prem or cloud ERP. Most businesses today prefer a cloud-based ERP to promote increased scalability and flexibility.
Implementation: Once you’ve chosen a solutions vendor, you need to assign a project manager who will oversee the implementation process which includes discussing employee trainings, project timeline and schedule to ensure your expectations are met. You will also need to consider creating a small implementation team to keep the project on track while ensuring adoption and buy-in across key departments.
Change management: Consider planning the transition with your workforce to help them understand the changes and how they would benefit from the implementation. The planning should also include comprehensive training and support to empower your team once you go live.
Gain Competitive Edge With Manufacturing ERP System
Quick responses to market changes are vital in your dynamic industry and the sole use of spreadsheet files could fail you. With ERP, you can get real-time insights to optimize production processes and meet customer demands. It's not just convenience; it's a necessity in your fast-paced environment.
With data accuracy critical in your line of work, an ERP platform for manufacturers acts as your ultimate data hub. Information from all your departments goes into one system, providing you with a single source of the definitive truth, where workbooks cannot suffice.
Significantly reduce errors, drive productivity and maximize operations—this means no more searching for reliable data or worrying about accuracy. A manufacturing ERP is a robust organization-wide solution that helps you:
Streamline processes: Manual processes like encoding data to spreadsheets are time-consuming and susceptible to the mistakes mentioned earlier. An ERP can streamline your operations by automating repetitive tasks and integrating workflows, minimizing human error whilst boosting performance.
Optimize the production line: Picture your production line—ERP software can orchestrate the entire process, from picking to packaging, helping to reduce cycle times and enhance overall efficiency.
Achieve scalability and flexibility: As your business evolves, your requirements also become more complex. Purpose-built ERP is built to adapt and grow with your manufacturing business. With the right system, you’re able to decide when you’re ready to add new functionalities as your operations expand. This scalability ensures that your ERP system delivers optimal ROI.
Establish a central platform: Think of ERP as your foundation. You start with the bedrock and construct your tech stack one piece at a time. Whether it's integrating new machinery, expanding your product line or integrating additional business software, an ERP system can easily adjust to your unique needs. This flexibility means your technology never holds you back.
Leverage real-time insights: As a leader in your industry, every decision you make counts. That's where up-to-date insights become indispensable. Utilize dynamic dashboards and reports that offer a bird's-eye view of your operational performance. With data at your fingertips, you can make informed decisions that drive your business forward.
Unlike spreadsheets, a manufacturing ERP allows you to track the progress of your orders, monitor resource utilization and identify bottlenecks—all in real-time. This level of data-driven decision-making empowers you to elevate your operations. An enterprise solution is like having a control tower overseeing your entire manufacturing process, ensuring you're always on track.
A Tailored Manufacturing ERP Can Transform Your Business
While we’ve listed some of the ways purpose-built ERP software can help your business succeed, it’s important to keep in mind that not all ERPs are the same. Choosing to implement an industry-specific ERP for manufacturers can revolutionize various aspects of your operations by offering features for the following:
Production planning: Manufacturing ERP informs schedules based on customer orders, reducing changeovers and enhancing efficiency.
Inventory tracking: Detailed tracking through barcode technology ensures accurate SKU counts and location awareness.
Materials requirement planning: Purpose-built ERP enables lean manufacturing with low on-site inventory, helping you to minimize carrying costs.
Supply chain management: Transact with supply chain partners via a secure digital platform in alignment with production schedules and component deliveries.
As demand increases in your evolving business, you need a robust solution without the limitations of spreadsheets—you need an ERP system. Unlike generic software, an industry-specific ERP can deliver features tailored to your industry and designed to solve the problems businesses like yours face on a daily basis.
For example, an ERP for discrete manufacturers has features that allow you to create flexible quoting for custom products, automatically generate bills of materials (BOMs) and analyze job variance including factors that affect profitability.
Meanwhile, process manufacturing ERPs provide recipe and formula management functionality to ensure consistent batch production and enhanced lot traceability to improve quality control and minimize waste, including compliance features to help ensure you’re always adhering to necessary regulations.
Moreover, if you’re ready to embark on your digital transformation journey, partnering with a vendor with decades of collective experience can help you with the process.
To discover more, we encourage you to check out these manufacturing ERP resources:
Read this blog to understand which manufacturing ERP software is the best fit for your business.
In this blog you’ll learn how an ERP can automate manual processes.
Discover the top five benefits of an ERP for process manufacturing.
Hear directly from our customers on how they increase automation and efficiency and drive growth and continuous improvement with Aptean manufacturing ERPs.
Aptean is proud to be a by-your-side solutions partner for all our customers—and better still, we really speak your language and know your industry.
Ready to elevate your manufacturing operations? Discover how, today.
Related Articles
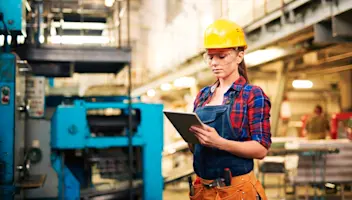

Bent u klaar om uw bedrijf radicaal te veranderen?
We hebben gespecialiseerde ERP-oplossingen waarmee u elke uitdaging in uw branche aankunt.
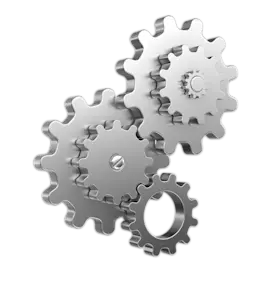