Why Food Traceability is More Important Now than Ever
Why Food Traceability is More Important Now than Ever
Why Food Traceability is More Important Now than Ever
29 Apr 2020
Aptean Staff Writer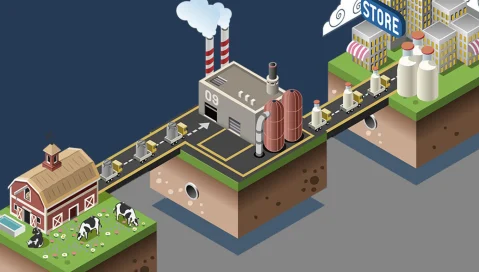
According to Allied Market Research, the global food traceability market is expected to garner $22.27 billion by 2025 (that’s an annual growth rate of 9.3% from 2018 to 2025). As today’s fragmented global food supply chains continue to become more complex, that number shouldn’t come as a surprise. Producing even the simplest food items in 2020 can include a huge number of contributors – from fertilizer manufacturers to farmers, processors to transporters – all of which have their own risks associated with their respective operations. That’s why it’s never been more important for food manufacturers and processors to put traceability and transparency at the forefront of their business by utilizing available technology to ensure the health and safety of consumers.
The Global Food Supply Chain
It’s estimated that 600 million people (or one in every ten people in the world) will fall ill from eating contaminated food every year. While food traceability efforts have increased globally, globalization of the food supply chain has made it extremely difficult to detect and prevent outbreaks of foodborne illness.
Think about this: 80% of the seafood consumed in the US is imported. A meat company located in the Amazon supplies most of the world’s fast-food chains with beef. Almost half of the apple juice consumed in the US comes from China. With 15% of the US’s food supply coming from sources outside of the country, the ability to successfully trace a particular ingredient or product down to its place of origin comes with a monumental set of logistical barriers.
While most developed countries have taken the initiative to put their own food safety protocols and regulations in place (either corporate or government-mandated), the same can’t be said for other high producing countries. Take asparagus or fresh mangoes from Peru, for example. Late last year, the FDA cited 70 Peruvian companies for exporting products containing illegal or undeclared substances, mislabeling, decomposition or contamination. These companies and their subsequent products (which also included hot peppers, fruit juice, soft drinks and evaporated milk) were prevented from entering the US market until they met the requirements put in place by the FDA. Though Peru does have procedures and guidelines in place to ensure the quality and safety of its exports, they may not be up to the same standards as other more developed countries.
It’s important not to neglect the issue of food globalization in times of worldwide turmoil, either. The novel Coronavirus, for example, will inevitably result in global disruption to international production and commercial channels. A scarcity of workers in the trucking, rail and shipping industries has resulted in global warehouses being stuffed to the brim with frozen and non-perishable foods, but no means to distribute it. Restrictions on migrant labor have increased internationally, affecting the way agriculture businesses and meat processors run their operations. And border and port closures are limiting the way countries are trading supplies, products and ingredients. This, of course, is all happening on the heels of an increase in climate change-related disasters, which will continue to wreak havoc on global food production in the coming years. As food safety standards continue to shift and be tested during these times of turmoil, will the world be able to properly adapt and ensure food security and safety? Only time will tell.
With the world so dependent on this global supply chain to deliver us so much of the food we consume every day, how do food manufacturers and processors ensure proper traceability measures in their factories and plants? According to some of the world’s most successful food companies, the answer is clear: with the help of technology.
Food Traceability Technology
While food traceability isn’t necessarily a new thing, in order to stay compliant in a global food environment, companies need to implement systems and tools that promote full end-to-end traceability.
But why is traceability so important for food manufacturers and processors? The ability to track ingredients bi-directionally through the supply chain not only reduces costs associated with recalls or contaminated products, but also instills consumer confidence in your brand and helps to enhance your company’s image. Today, fewer than one in four consumers in the US trust labels on food packaging. That number is alarming and possibly detrimental to food companies who aren’t ensuring proper transparency and traceability within their supply chain. In order to decrease the skepticism of the modern consumer, food manufacturers and processors must implement the proper tools to ensure end-to-end food safety.
Technology like barcoding, for example, is widely used by food companies because of its cost-effectiveness and ability to integrate with more robust systems like a food enterprise resource planning (ERP) solution. In terms of global product tracking, barcoding makes use of Global Trade Item Number (GTIN) to properly and efficiently track items throughout the global supply chain. These GTIN numbers are governed by GS1, a not-for-profit organization that develops and maintains global standards in supply chain business communication, helping to ensure world-wide communication and collaboration. In the event of a recall, an ERP solution with barcoding technology allows food manufacturers and processors to peel back each level of production to see where an error has been made and where that material in question has gone to next. This technology gives you the ability to track at the item, lot, serial or container level within a single interface, providing you with all the information you need to perform a full recall in under 60 seconds if necessary.
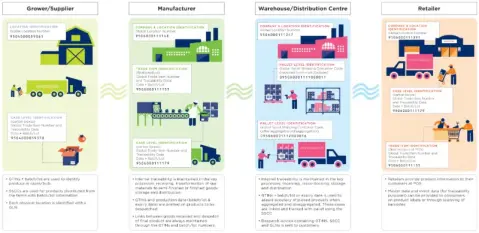
For food manufacturers and processors looking to streamline their operations and improve food safety, an all-in-one system built for the food industry can help. Solutions like an ERP system provide companies with a holistic view of food safety and include features like built-in quality procedures at various stages of material movement, full food safety reporting and document retention, and lot number tracking at all levels of production.
Aptean Food & Beverage ERP JustFood Edition allows you to capture the data and processes needed to meet safety standards and ensure quality and control over your food products. If you’d like to learn more about our food ERP solution, reach out to us now.
Inzicht in voedsel
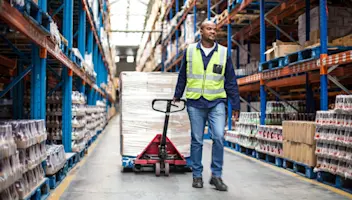
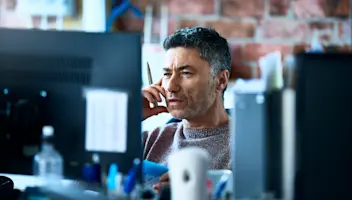
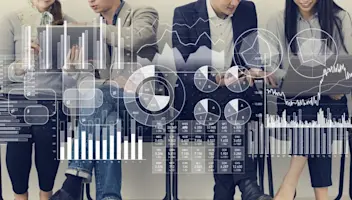
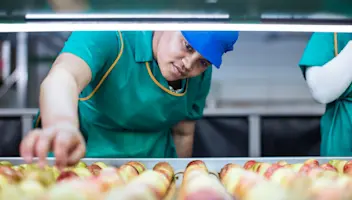
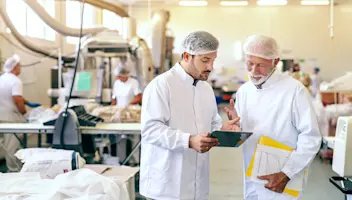
Wilt u weten wat we voor uw voedingsbedrijf kunnen betekenen?
Wij helpen u graag. Neem contact met ons op en ontdek welke smaken we te bieden hebben.
