Seamless Traceability.
Flawless Audits.
Each Time. Every Time.
Why You Need a Digital QA System
Operationally, food safety systems are being increasingly tested because of more stringent regulations, high customer purchasing standards and skills shortages.
You need to provide traceability and compliance reporting and flawless audit information within set timelines. Paper based, error prone and time-consuming processes just don’t stand up to these demands so it is essential that food manufacturers are equipped with proactive tools to pre-empt and mitigate likely issues on the factory floor, as well as maintaining efficient food safety and traceability processes and transparent audit systems.
Digitalising your QA processes delivers improved efficiency and insights to:
Minimise administration time and maximise reporting value
Accelerate and enhance food safety processes
Make dynamic business decisions
Be audit ready, reduce costs and more
Aptean Food and Beverage QA Management
Industry-leading shop floor data capture and reporting, incorporating precise forward and backward traceability, will provide:
Real-time auto-alerts and non-conformance management, delivered in a range of formats and channels including email and SMS
Design and test capabilities and deploy bespoke digital procedures and condition-based workflows
Digital tracking accounts for every raw material and product – from intake through to packing and distribution
Support of consignment mixing, throughout all process and packing phases
Dynamic traceability reporting delivers audit traces in seconds
Centralised real-time reporting and dashboards
Success with Aptean
Bearfields of London Achieve Their Vision for a Paperless Business.
Bearfields of London are an award-winning UK processor and producer of pork products, including gammons and hams. With their current system not meeting their requirements, they were reliant on paper to manage QA procedures, leading to a lack of transparency and visibility across their business.
Recognising that digitalisation would eliminate paper-based QA and manual errors from their operations, they turned to Aptean. Since implementing Aptean QA Management, Bearfields has improved QA and traceability with 100% transparency across all 5 sites and have removed paper entirely from their business.
“All of our technical and QA procedures are now paperless; we have real-time visibility on checks, non-conformances, and corrective actions.” - Neil Edwards, Operations Director, Bearfields
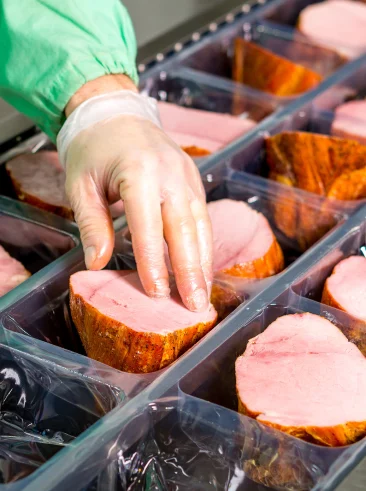
Bi-Directional Traceability
Based on decades of experience, working directly with food manufacturers, our quality assurance management software delivers QA integrity and superior visibility—from raw materials to outbound retail products.
With Aptean Food & Beverage QA Management, you will have the proof to demonstrate that each carcass, raw material type or ingredient used, can be matched to the finished products at the end of the processing line, and fast reporting capabilities for audit and compliance requirement when you need it.
Legal and compliance checks occur in real time, with flags, escalation and line stop capability, preventing significant food safety issues from ever leaving the factory.
Capture real-time factory floor data, via android mobile devices, rugged tablets, touchscreens and PCs, evidencing that all quality checks have been made at the correct time and place.
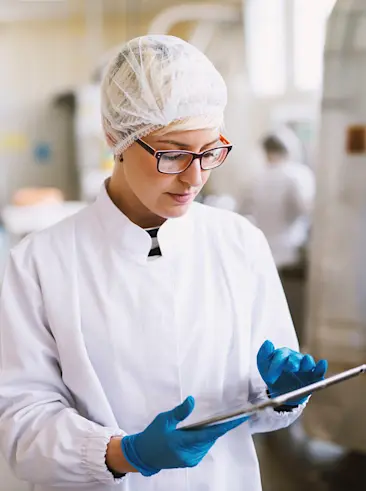
Why Aptean Food & Beverage QA Management?
Empower your QA experts to design, test and deploy your own digital procedures.
Eliminate paper-based QA reporting and ensure unbroken bi-directional traceability for auditing purposes.
With our instant data retrieval and dynamic reporting, provide seamless traceability throughout the food factory.
Digitally track and account for everything—from intake, batch, stock, value-added production, packing, through to distribution.
Deliver flawless audit data in minutes, including mass balance reporting in seconds, whenever the auditor calls.
Step up to QA digitalisation that’s proven to deliver cost savings.
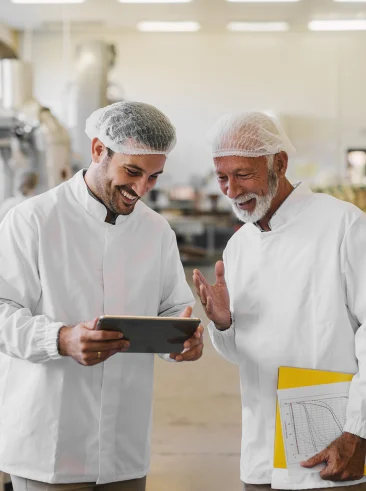
Increase Process Control.
Improve Integrity.
Data Capture
Show how many checks have been performed by capturing whenever and wherever checks have happened, whilst identifying all non-conformances.
Operator Checks
Evidence operator check completion at prescribed time intervals, short interval control points and CCPs.
Stock Integrity
Automatically put stock on hold at any manufacturing stage, for follow up QA checks.
Quarantine Control
Control quarantined items to prevent cross-contamination and manage any rejects.
Ensure Compliance
Minimise non-compliances for both customer and regulatory standards, through digital validation and safeguarding.
Aptean Insights
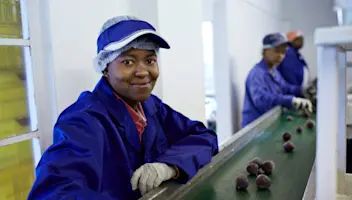
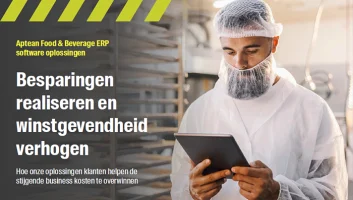
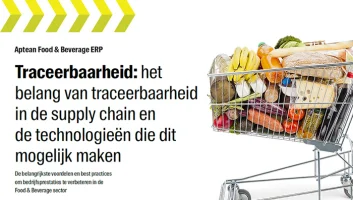
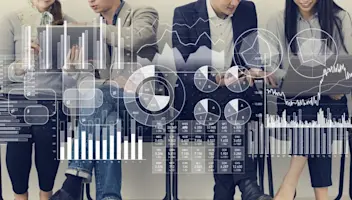
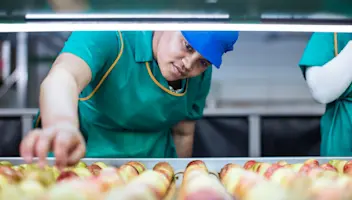
Wilt u weten wat we voor uw voedingsbedrijf kunnen betekenen?
Wij helpen u graag. Neem contact met ons op en ontdek welke smaken we te bieden hebben.
