Destacado en este post
The Starter Guide To Manufacturing Software: Everything You Need To Know
The Starter Guide To Manufacturing Software: Everything You Need To Know
17 Ene 2024
April Matthews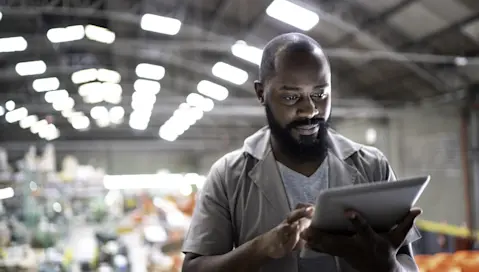
With every industry publication, email blast, conference and social media post focused on the topic, there’s no escaping the fact that your business must prioritize digital transformation and invest in cloud-based manufacturing technology. They are now simply must-haves to remain competitive.
But the notion of a perfect digital transformation journey falling into place is far from the reality that faces most busy manufacturers. You’re likely plagued with many questions and wondering where to start, or how to build on what you’ve already got without disrupting your business.
There are so many manufacturing software solutions on the market, each offering capabilities for different aspects of your business, with some seemingly overlapping in their scope, that deciding how to progress can get overwhelming very quickly. And that’s not even mentioning the variety of vendors, deployment methods and license models on offer. To help you avoid decision paralysis and get to improving your business performance right now, we’ve put together this guide on all things manufacturing software. We’ll cover the basics here—from challenges it can solve and the features offered, to common systems and vendor considerations—and dive into more detail in future blogs.
So be on the lookout for more content, and in the meantime, let’s start to unpick the complex web that is manufacturing software.
What Is Manufacturing Software?
Simply defined, manufacturing software is any digital system that helps your business optimize its manufacturing operations.
Many different solutions make up the manufacturing software landscape, and each plays an important role, but slotting all the pieces together is where they truly shine, acting as one seamless ecosystem to boost performance from product ideation, through production to customer delivery. When chosen wisely and implemented correctly, manufacturing software streamlines processes, reduces costs, optimizes production and enhances customer service to improve profitability and accelerate the growth of your business—no matter what industry vertical you operate in. As to which manufacturing software systems you’ll need? Well, that depends on your business requirements, but we’ve provided a list of common solutions below as well as some guardrails to help you choose the technology that will future-proof your business operations.
Challenges Solved With Manufacturing Software
Staying on top of your game requires overcoming numerous hurdles that could impede your growth—whether that’s common operational challenges or current industry trends. Here is just a snapshot of the problems facing manufacturers in today’s market that mean you simply must focus on implementing a solid digital transformation strategy that includes deploying the right manufacturing technology.
Current and Emerging Manufacturing Trends
Rising cost of doing business – With factors like inflation, the rising price of raw materials, increasing labor expenses and costly energy bills, your profit margins are under pressure. Manufacturing software can help you reduce operational costs, boost profitability and protect your bottom line.
Supply chain disruptions – Transportation delays, component shortages, ongoing geopolitical conflicts and many other issues are disrupting the global supply chain, but advanced supply chain software can give your business the agility to adapt, overcome and grow.
Changing consumer trends – Customer preferences have, and always will, shift over time, but with social media and more exacting consumers driving change at a rapid rate, your business needs to be ready to react now more than ever. Whether it’s responding to demands for greater diversity in cosmetics, improved logistics sustainability or more plant-based food options, manufacturing software helps improve product ideation processes, accelerate time-to-market and deliver customer satisfaction.
Labor shortages – The global talent shortage is going nowhere. In a report from Deloitte the projection is stark: by 2030, an estimated 2.1 million manufacturing jobs are expected to remain vacant in the U.S. alone. Implementing the right technology will be a crucial strategy to help your business automate processes and maximize existing resources to combat continuing labor shortages.
Demands for sustainability – Whether it’s from environmentally-conscious consumers or government legislation, the pressure for manufacturing businesses to improve their sustainability initiatives is only increasing. From responsible sourcing and production, to reducing waste and optimizing your transportation carbon footprint, technology can help your business deliver.
Common Operational Manufacturing Challenges
Lack of visibility – Whether it’s caused by disparate systems, outdated spreadsheets, manual processes or disjointed integration, a lack of accurate, real-time information can cause problems across your organization. But, with the right manufacturing software ecosystem, you can say goodbye to data siloes and hello to end-to-end visibility—helping you make smarter, data-driven decisions.
Inaccurate forecasting and planning – Precisely predicting demand and managing inventory and production planning to accommodate it is a complex task that can easily go awry—increasing waste or leading to delayed orders and missed revenue opportunities. This makes the demand forecasting and production planning capabilities some of the most crucial that manufacturing software can offer, helping you reliably predict and meet demand.
Customer satisfaction inconsistency – To ensure brand loyalty and protect your profitability, you must be able to deliver on customer promises, each and every time. From product design and quality management to order fulfillment and delivery scheduling, the right manufacturing systems can help you ensure customer satisfaction at every step.
Failure to meet schedule attainment goals – Unplanned downtime, equipment malfunctions, misaligned maintenance schedules—there are many factors that can cause you to miss production goals. Thankfully, there are also manufacturing software solutions designed to help you maximize equipment utilization and plan attainment.
Compliance struggles – No matter what industry you operate in, you must comply with strict regulations and standards. And ensuring you have all the necessary processes, alerts and documentation in place to remain compliant, even as rules evolve, can be time- and resource-intensive. Manufacturing software eases that burden and can automate many of these critical processes.
To tackle all of these bumps in the road, you’ll need to carefully plan your digital transformation and implement the right manufacturing software solutions to address your most pressing challenges.
Must-Have Features of Manufacturing Software
Now that we’ve looked at why you should be considering manufacturing software, let’s dive into exactly how it can help you overcome your challenges.
Whether you’re looking for your first system, considering updating a legacy solution or deciding which piece to add to your tech stack next, below are some of the must-have features a complete manufacturing software platform should deliver.
Fully integrated digital repository – By centralizing vital data within a unified and seamlessly integrated ecosystem, your entire organization benefits from a single source of truth—improving internal communication, boosting collaboration and enabling data-driven decision-making.
Comprehensive material traceability – Centralized platforms offer bidirectional visibility across your supply chain, encompassing inbound and outbound shipments, as well as the movement of materials and products within your facilities. These capabilities enable precise tracking down to the individual item level, even tracing the components comprising final products.
Efficient inventory management – Having a clear picture in real time of your current stock levels of finished products and raw materials, including reordering, is pivotal. Inventory management functionality can capture all supply updates, facilitating real-time monitoring of stock levels to support prompt replenishment.
Accurate demand planning and forecasting – Leveraging historical sales data and recent purchasing trends, manufacturing platforms deliver reliable predictions for material requirements and production targets, aligning with demand fluctuations.
Streamlined new product development (NPD) – Utilizing purpose-built tools for product development, testing and project management helps your business accelerate time to market for your latest offerings. That way, you can beat competitors to the punch, capture a larger slice of the market and drive profitability.
Optimized transportation operations – Gaining real-time visibility and full control over your entire transportation operation—from optimizing route plans to perfecting final mile delivery—reduces logistics costs while enhancing customer service during this crucial stage.
Performance tracking and analytics – Whether it’s tracking financial data, monitoring planned vs. actual production output or keeping tabs on real-time delivery progress, manufacturing software provides reports and intuitive visualizations of your key performance indicators (KPIs) to help you analyze progress and implement improvements based on these insights.
Manufacturing software systems equipped with these must-have functionalities are pivotal in strengthening supply chain resilience for all manufacturers. But your business is unique and will require additional capabilities tailored to your industry challenges. That’s where specialized solutions comes in.
Opt for Industry-Specific Software Instead of Generic System
When it comes to selecting the best manufacturing solutions for your business, one of the most crucial decisions is choosing between generic and industry-specific software. Before we explore the various types of software or specific solutions you may consider, it's essential to differentiate these two options.
Generic software – Takes a one-size-fits-all approach to appeal to as many businesses as possible and deliver “good enough” features to satisfy common basic needs. However, many of these generic systems fall short of addressing the unique challenges of particular industries and business types, leading to inefficient workarounds, costly customizations and lower return on investment (ROI). Many businesses find themselves quickly outgrowing generic options and needing to replace or upgrade their software within a few years, hindering your business from reaching its full potential as quickly.
Industry-specific software – Encompasses the standard must-have features as well as capabilities tailored to your sector’s unique needs and nuances—providing additional benefits not available with generic options and unlocking rapid ROI. The best industry-specific software is also designed and supported by experts that know your industry inside out, meaning you benefit from best practice knowledge and can be sure the software will evolve in line with your industry requirements.
Both options deserve consideration, but most modern businesses are opting for industry-specific software because of its ability to improve precision and adaptability—empowering them to stay agile and gain a competitive edge.
The choice is clear: for manufacturing leaders like you, the path to success is paved with industry-specific solutions.
Here are a few examples of how specialized solutions can benefit specific industries:
Discrete manufacturing – For discrete and industrial manufacturers, software helps you effortlessly create and manage bill of materials (BOMs), optimize production planning and scheduling, manage shop floor operations, tackle complex job costing to improve margins and maintain strong customer relationships throughout the sales and service lifecycle.
Process manufacturing – Allows you to better manage complex product recipes and formulations to improve batch consistency and quality control as well as providing full lot traceability to improve visibility and optimize product recall procedures. Particularly important for process manufacturers in highly regulated industries, manufacturing software also enhances compliance and reporting with additional checks and documentation management.
Food and beverage – Specialized food software offers a range of features tailored to the challenges of your industry, from food traceability and recipe management, to allergen management and food safety. In addition, some solutions offer benefits for specific sub-verticals, such as precise catch weight management for meat and dairy businesses.
Fashion and apparel – Whether it’s helping your accelerate time-to-market, streamline fashion supply chain management, master omnichannel fulfillment, make strides toward sustainability goals or perfect product creation to delight your customers, software designed for the fashion and apparel industries can improve your operations end to end.
Cloud vs. On-Premise Deployment: Future Proofing Your Tech Stack
As well as deciding between generic and industry-specific solutions, you’ll also need to choose whether you deploy each of your solutions on-premise or in the cloud. While cloud software is a cornerstone in most manufacturing digital transformations, you’ll still need to make the right choice for your business. So, let’s take a quick look at the options.
With cloud software, each system is hosted on remote servers and accessed anywhere through an internet-connected device. Typically, the provider manages maintenance, staffing, backups and updates on your behalf—24/7.
Conversely, when software is hosted on-premise, your business is entirely responsible for the hosting. This means you’ll need to allocate space on-site for your server and hire an in-house team to handle all IT-related tasks, such as software maintenance, upgrades and security. In addition, accessibility is limited as staff either need to be on-site or use a virtual private network (VPN) to access the system.
Many businesses like yours consider cloud-based manufacturing software because it’s:
More cost-effective as it negates the need for hardware ownership and maintenance.
Easy to scale up or down as necessary, while on-premise solutions are often more complex and costly to adjust.
Quicker to deploy, without the need for large server installation and configuration.
In a digital transformation strategy, opting for cloud-based solutions is crucial to future-proofing your business. Cloud technologies offer scalability, remote accessibility, data security and cost-efficiency, ensuring your company stays agile and competitive.
Types of Manufacturing Software To Consider
A quick Google search will provide you with a whole alphabet soup of three-letter software systems and potential platforms to choose from. And you’re probably left wondering: Do I need all of these systems? What do they do? Is there any overlap? Are they all suited to manufacturers? Which ones are most important?
To help you make sense of that onslaught of information, we’ve listed some of the most frequently implemented solutions that you should consider depending on your business requirements and operational goals.
And, while you may be looking to deploy all of these systems as part of your digital transformation journey, remember it’s a marathon, not a sprint. There doesn’t need to be a ton of pressure and you can build your tech stack step by step. With that in mind, let’s kick off the list with the most common first step—enterprise resource planning software.
Enterprise Resource Planning (ERP)
Enterprise resource planning (ERP) is a comprehensive solution that allows you to manage procurement, finance, production, inventory and order management. As a result of its all-encompassing nature and ability to provide a single source of truth across the entire operation, many businesses choose to implement ERP as their core or foundational platform—integrating other systems into the ecosystem one by one once their ERP is in place.
By centralizing core business functions on a single platform, a manufacturing ERP standardizes and improves your processes, empowers your team by simplifying or automating everyday tasks and provides real-time visibility of your entire supply chain.
All of this means improved efficiency, faster and smarter decision-making, reduced costs, better customer experiences and improved profitability. Plus, with an industry-specific ERP package, you’re able to take advantage of specialized features to solve niche industry challenges, all from one system.
The following robust solutions are building blocks that complement and enhance your ERP’s capabilities, ensuring your manufacturing operations remain competitive, efficient and resilient as your business evolves.
Product Lifecycle Management (PLM)
If you’re designing and manufacturing your own items, PLM software is a pivotal organization-wide platform to help you manage the entire new product development (NPD) process. By centralizing your data, a PLM system aids collaborative design, development, manufacturing marketing, packaging and compliance.
With features to standardize product data across your organization, capabilities to improve recipe, formula and BOM management, and quality and compliance tools, PLM offers tools for teams throughout your business—streamlining end-to-end product processes and improving collaboration.
PLM can help you reduce time to market, improve product quality, tightly control costs and ensure regulatory compliance, making it an indispensable tool for businesses of all sizes navigating the complete product lifecycle.
Enterprise Asset Management (EAM)
Maximizing the full potential of your manufacturing assets is essential whatever you’re producing. Enterprise asset management (EAM) software offers a centralized hub for asset information, encompassing their condition and maintenance history.
Asset tracking, maintenance planning, work order management, inventory oversight and data-driven reporting are EAM’s core functions, giving your managers and maintenance crews everything they need to manage the full lifecycle of your equipment and maximize asset utilization.
By giving you the ability to predict asset behaviors and proactively approach maintenance schedules, EAM significantly helps reduce downtime, enhance performance, extend asset life, realize cost savings and ensure compliance.
Overall Equipment Effectiveness (OEE)
Most manufacturers will be familiar with OEE as a metric: measuring actual performance against available planned production time. OEE software then, is the system used to both easily calculate this metric and facilitate improvements to your score—identifying issues and driving continuous improvement.
The best OEE software offers direct integration with equipment to provide visibility into real-time performance stats, intuitive visualizations of where issues are arising, and cost and profitability monitoring.
The benefits of these OEE capabilities include reduced downtime, consistent plan attainment, improved yield management, more assured order fulfillment and heightened customer satisfaction.
Transportation Management System (TMS)
TMS software can cover a broad range of functionalities depending on your business needs, but the focus should be to enhance your end-to-end distribution operation—reducing costs while improving customer satisfaction. To do this, there are three crucial capabilities: route optimization, live execution management and electronic proof of delivery.
Together, these TMS capabilities enable you to plan, execute and monitor your logistics operations efficiently. You’re able to centralize transportation data for real-time visibility, reduce planning time and optimize routes, eliminate delivery paperwork, and control live delivery execution.
This means that any manufacturing business running their own distribution operation should implement TMS tools to significantly reduce transportation costs, enhance distribution visibility, improve resource utilization and enhance customer service.
Business Intelligence (BI)
BI software consolidates all of your business data and standardizes your reporting processes to deliver greater transparency and insights into performance across your operation.
With BI tools you’re able to use dashboards and reporting capabilities to bring your data to life and uncover hidden trends and relationships—allowing you to easily analyze information, identify areas for improvement, make smart data-driven decisions and drive continuous improvement. Whether you’re using it to boost efficiency, improve customer service, or cut unnecessary operational costs, an advanced BI solution is pivotal to your strategic growth.
And what’s more, choosing industry-specific BI tools can offer further benefits by providing KPIs out of the box that are tailored to your industry challenges to give you more granular data visibility and help you reach ROI more quickly.
The Advantages of Sourcing Manufacturing Solutions From a Single Vendor
In software implementation projects, the vendor you choose to partner with is often just as important as the solution itself. And in this regard, many successful businesses share a common strategy when navigating their digital transformation journey. The secret? Sourcing their technology from a single, trusted vendor.
Below are some of the benefits of partnering with a single software provider:
Seamless integration – When you invest in a comprehensive manufacturing suite, you can achieve seamless integration between all components, fostering an ecosystem where your systems work harmoniously.
Reduced complexity – You can avoid the hassles of managing multiple vendors and associated contracts, support channels and updates.
Dedicated support – Expert support teams are well-versed in all suite components, ensuring your organization receives timely and knowledgeable assistance.
Scalability – As your business grows, you can seamlessly scale up by adding additional modules, systems or services from the same vendor, ensuring your entire software ecosystem evolves with your business.
Cost savings – Reducing complexity and eliminating integration issues can lead to significant cost savings in the long run.
While the availability of cloud solutions is a major factor when evaluating vendor partners, you also need to assess both their industry and technical expertise and determine if the solutions they offer would align with your business needs. To explore these factors consider inquiring about their in-house development and roadmap for future enhancements, scheduling product demos to see the software in action, and seeking testimonials and success stories from other customers in your industry.
Selecting the right partner can ensure ease of implementation, accelerate ROI and future-proof your technology stack—all driving business growth more quickly.
Start Building Your Manufacturing Tech Stack to Future-Proof Your Business Today
Consider your tech stack as the foundation upon which your digital transformation efforts are built. Ideally, the combination of technologies and tailored software solutions your organization leverages should help improve overall operational efficiency, customer satisfaction and most of all, your bottom line. So, making the right choices is pivotal.
Hopefully, the information we’ve provided above gets you off to a great start on choosing the right systems for your business, but you’re also going to need the right partner. Enter Aptean.
Here at Aptean, we combine best-of-breed manufacturing software systems with a collaborative approach to implementation and support, ensuring we can be by-your-side partners to our customers. Our industry-specific software suite is available in the cloud on the Software as a Service (SaaS) model providing easy-to-use interfaces and specialized functionality to give you the agility you need to continuously satisfy unique and evolving customer demands while controlling operational efficiency.
We’re relentless in fostering enduring partnerships throughout your digital transformation journey. Our unwavering commitment is evident in the constant evolution of our solutions and dedicated approach to support. Together, we propel you toward lasting success. That’s the Aptean advantage.
But don’t just take our word for it—check out some of our customer success stories, find out more about our manufacturing software or request a personalized demo.
¿Todo listo para transformar tu negocio?
Tenemos el software especializado en tu sector que ayudará a tu organización a prosperar.
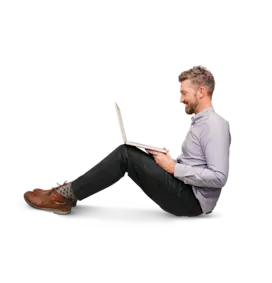